As a hiring manager, finding the right manufacturing engineer is crucial to driving efficiency in production processes. Manufacturing engineers play a key role in optimizing operations, reducing costs, and ensuring product quality. However, companies often struggle with identifying the right qualifications and skills needed for this role, leading to mismatches and inefficiencies.
In this article, we will guide you through the entire hiring process for manufacturing engineers. From understanding their roles and responsibilities to sourcing and assessing candidates, you will find detailed insights and practical advice. Be sure to check out our manufacturing engineer job description for more information on crafting an effective job listing.
Table of contents
Why Hire a Manufacturing Engineer?
A Manufacturing Engineer can solve production challenges and optimize processes. They might address issues like low product quality, high production costs, or inefficient workflows that are holding back your manufacturing operations.
Consider hiring a Manufacturing Engineer when you need to:
- Improve production efficiency and reduce waste
- Implement new manufacturing technologies or automation
- Design and optimize production lines
If you're unsure about committing to a full-time hire, start with a Manufacturing Engineer skills assessment to evaluate potential candidates. This can help you determine if their expertise aligns with your specific manufacturing needs before making a long-term decision.
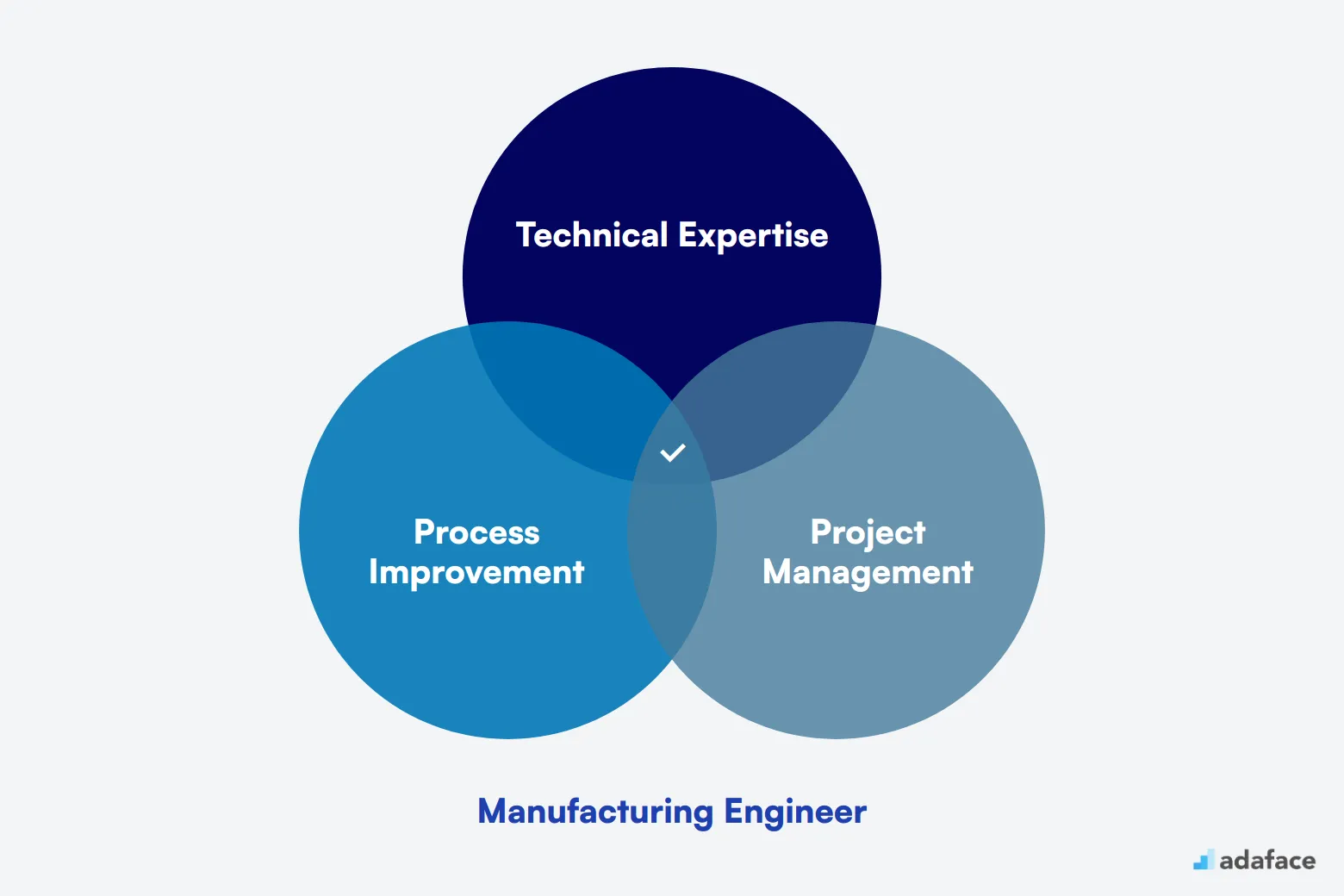
What Does a Manufacturing Engineer Do?
A Manufacturing Engineer plays a key role in designing, implementing, and optimizing manufacturing processes. They work to improve product quality, reduce costs, and increase efficiency in production facilities.
The day-to-day responsibilities of a Manufacturing Engineer include:
- Analyzing production data and workflows to identify areas for improvement
- Designing and implementing new manufacturing systems or processes
- Troubleshooting equipment issues and coordinating maintenance
- Ensuring compliance with safety regulations and quality standards
- Collaborating with other departments to streamline production
- Training production staff on new processes or equipment
Manufacturing Engineer Hiring Process
The hiring process for a Manufacturing Engineer role is a structured approach designed to identify candidates with the right mix of technical skills and problem-solving abilities. The timeline can vary, but typically, it takes around 1-2 months from start to finish.
- Define the role: Begin by crafting a detailed job description for a Manufacturing Engineer to attract the right candidates. Post it on relevant job boards and company websites.
- Resume screening: Within a week, you should start receiving applications. Screen resumes to shortlist candidates who meet the specified requirements.
- Skills assessment: Conduct skill tests using an online assessment platform to evaluate candidates' technical abilities. This step can take about a week to administer and review.
- Interviews: Invite shortlisted candidates for interviews to assess cultural fit and deeper technical knowledge. This typically involves multiple rounds including technical and HR interviews.
- Final selection and offer: Choose the best candidate and extend an offer. Allow time for negotiation and acceptance.
Overall, the process is designed to identify the best talent while maintaining a smooth and efficient timeline. Each step is crucial to ensure you hire a candidate who not only meets the technical requirements but also fits well with your company culture. We'll explore each stage with more detailed insights in the following sections.
Key skills and qualifications for a Manufacturing Engineer
Creating the ideal candidate profile for a Manufacturing Engineer can be tricky. It's important to distinguish between must-have skills and nice-to-have qualifications. This helps in focusing on candidates who can hit the ground running while still leaving room for growth and specialization.
Required skills typically include a strong technical background, hands-on experience, and problem-solving abilities. Preferred qualifications often encompass advanced degrees, leadership experience, and familiarity with specific methodologies or systems.
To assess these skills effectively, consider using skills assessment tools that can objectively evaluate a candidate's technical proficiency and problem-solving capabilities.
Required skills and qualifications | Preferred skills and qualifications |
---|---|
Bachelor's degree in Mechanical, Industrial, or Manufacturing Engineering | Experience with Lean Manufacturing principles |
Minimum of three years' experience in manufacturing or production engineering | Familiarity with Six Sigma methodologies |
Proficiency with CAD software, such as AutoCAD or SolidWorks | Master's degree in a related field |
Strong problem-solving skills and attention to detail | Experience with ERP systems, such as SAP or Oracle |
Knowledge of manufacturing processes and equipment | Proven leadership and project management skills |
How to Write an Effective Manufacturing Engineer Job Description
Once you've outlined the ideal candidate profile, it's time to craft a job description that attracts top manufacturing engineering talent. A well-written Manufacturing Engineer job description can make all the difference in your hiring process.
Here are some tips to create a compelling job post:
- Highlight key responsibilities: Clearly outline the role's impact on production processes, cost reduction, and quality improvement. Mention specific tasks like developing manufacturing methods and implementing automation technologies.
- Balance technical and soft skills: List required technical expertise such as CAD software proficiency and knowledge of lean manufacturing principles. Also emphasize soft skills like problem-solving, teamwork, and communication abilities.
- Showcase your company's USP: Highlight unique aspects of your organization, such as cutting-edge projects, opportunities for professional growth, or a collaborative work environment. This helps your job posting stand out and attract passionate candidates.
- Be specific about qualifications: Clearly state required education (typically a bachelor's degree in Manufacturing or Industrial Engineering), years of experience, and any preferred certifications or specialized knowledge relevant to your industry.
Top Platforms to Source Manufacturing Engineers
Now that you have a well-crafted job description, it's time to post it on job listing sites to attract qualified Manufacturing Engineer candidates. The right platform can significantly impact the quality and quantity of applicants you receive. Let's explore some of the best options available for sourcing top talent in this field.
LinkedIn Jobs
Ideal for finding full-time Manufacturing Engineer positions across various industries. Offers extensive networking capabilities and detailed company profiles.
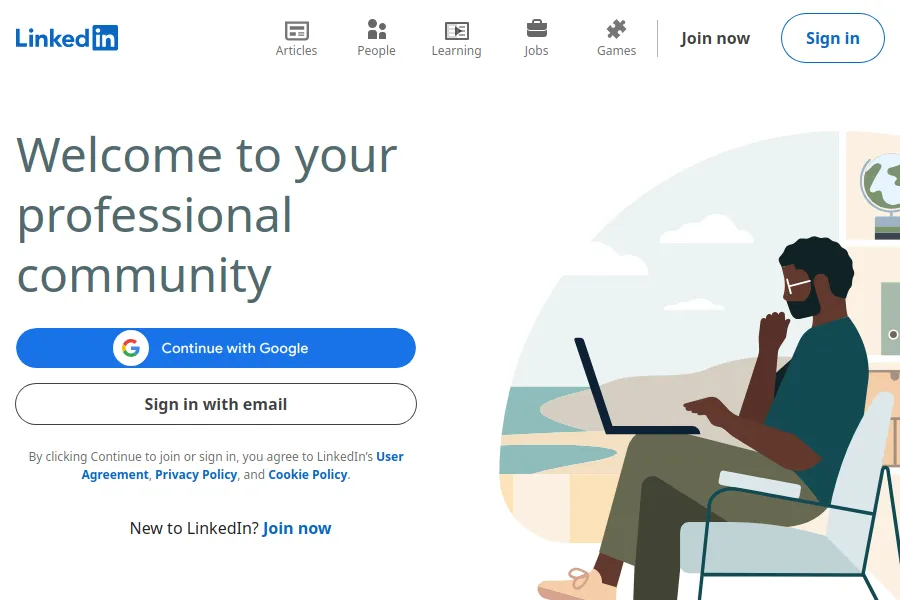
Indeed Manufacturing Engineer Jobs
Comprehensive job board for all types of Manufacturing Engineer positions. Offers a wide range of filters and easy application process.
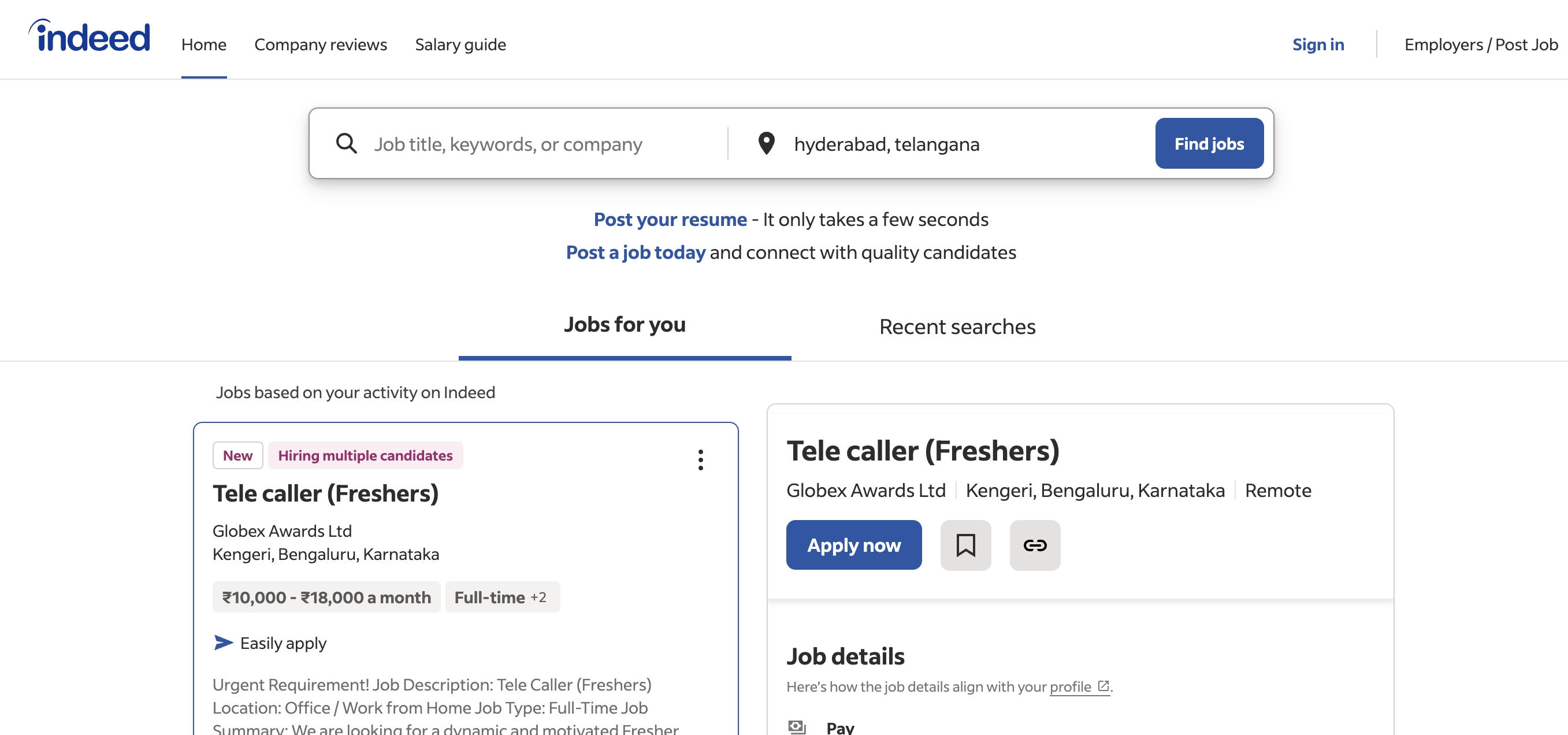
Glassdoor Manufacturing Engineer Jobs
Useful for full-time positions with added benefit of company reviews and salary information. Helps in understanding company culture and employee satisfaction.
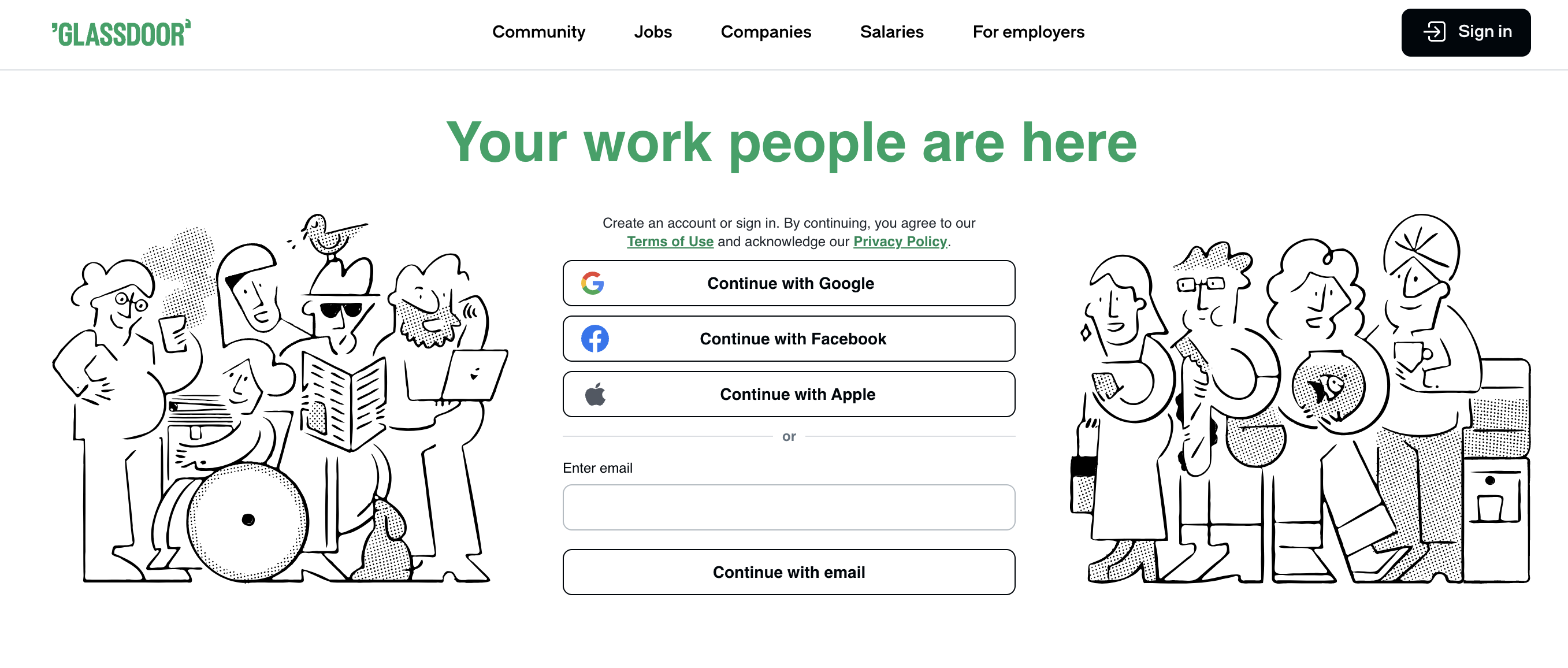
Beyond these popular sites, there are specialized platforms that cater specifically to engineering roles or offer unique features for recruiters. These include EngineerJobs for targeted searches, Dice for tech-focused positions, and SME Job Board for industry-specific connections. For project-based or temporary needs, Upwork's freelance platform can be a valuable resource. Each of these sites offers distinct advantages, so consider your specific requirements when choosing where to post your Manufacturing Engineer job listing.
Key Phrases to Spot in a Manufacturing Engineer's Resume
Screening resumes is a smart way to narrow down your pool of potential Manufacturing Engineers before diving into interviews. By focusing on resumes first, you can filter out candidates who don’t meet the basic qualifications, making your recruitment process more manageable.

The key to manual resume screening is to identify the must-have skills and qualifications. For a Manufacturing Engineer, look for keywords like ‘Bachelor's degree in Mechanical, Industrial, or Manufacturing Engineering’, experience with CAD software like AutoCAD or SolidWorks, and knowledge of manufacturing processes. Shortlist those that align with your essential criteria, ensuring a more relevant candidate pool for your next steps.
Alternatively, consider turning to AI and tools like Adaface's skill assessment tools. These AI models can scan through resumes to match job descriptions based on the keywords you provide. This can save time and bring accuracy to your screening process by highlighting the most suitable candidates.
Here's a detailed prompt you could use for AI screening tools:
TASK: Screen resumes to match job description for Manufacturing Engineer role
INPUT: Resumes
OUTPUT: For each resume, provide following information:
- Email id
- Name
- Matching keywords
- Score (out of 10 based on keywords matched)
- Recommendation (whether to shortlist this candidate or not)
- Shortlist (Yes, No or Maybe)
RULES:
- If unsure, list the candidate as Maybe instead of No
- Keep recommendations concise.
KEYWORDS DATA:
- Manufacturing processes (Lean Manufacturing, Six Sigma)
- Technical skills (CAD software, CAM software, PLC programming)
- Project management (project scheduling, risk management)
Recommended Skills Tests to Screen Manufacturing Engineers
When it comes to hiring Manufacturing Engineers, skills tests are a recommended approach to evaluate candidates' technical abilities objectively. These tests can help identify candidates with the right mix of technical and problem-solving skills that are necessary for the role.
Technical Aptitude Test: Manufacturing Engineers need a strong grasp of various technical concepts. Use Technical Aptitude Tests to assess candidates' understanding of mechanical and electrical principles, which are often important in this field.
Problem-Solving Test: Manufacturing Engineers regularly face challenges in production processes. The Problem-Solving Test evaluates candidates' ability to analyze issues and devise practical solutions, a key aspect of their daily responsibilities.
Attention to Detail Test: Precision is vital in manufacturing settings. The Attention to Detail Test ensures candidates can spot minor errors or inconsistencies, which can prevent costly mistakes in manufacturing processes.
Logical Reasoning Test: Many engineering problems require logical thinking. The Logical Reasoning Test helps determine if candidates can logically approach engineering problems and strategies.
Role-Specific Tests: Tailoring assessments to specific roles can be invaluable. Consider Role-Specific Tests that focus on skills directly linked to the Manufacturing Engineer role, ensuring a more precise evaluation.
How to Structure Interview Stage for Hiring Manufacturing Engineers
Candidates who have successfully passed the skills tests are ready to move onto the technical interview stage. This phase is crucial for assessing their hard skills and determining the best match for the role. While skills tests help filter out unfit candidates, technical interviews provide a unique platform to gauge the specifics of their abilities and practical knowledge. Let's review some sample interview questions that can enhance this process.
- What manufacturing processes are you most experienced with? This question helps to understand the candidate's hands-on experience and relevance to your specific manufacturing needs.
- Can you describe a challenging engineering problem you solved? This gives insight into problem-solving skills and the candidate’s ability to handle complex situations.
- How do you ensure quality control in your projects? This links to assessing their role in maintaining standards and highlights their understanding of quality assurance.
- What tools and software do you prefer using for engineering tasks? This question assesses their proficiency with modern tools and adaptability to different technologies.
- How do you prioritize tasks when managing multiple projects? This reveals their organizational skills and ability to handle pressure effectively.
What are the hiring costs for a Manufacturing Engineer?
Hiring a Manufacturing Engineer involves several costs beyond just salary. In the United States, the average salary is approximately $90,812 per year, but total costs can include recruitment expenses, onboarding, and benefits, which can add an additional 20-30% to the base salary. Depending on experience and location, the total cost to hire can vary significantly from $75,000 to over $160,000.
Manufacturing Engineer Salary United States
In the United States, the average salary for a Manufacturing Engineer is approximately $90,812 per year. Salaries can range from around $62,326 on the lower end to $123,271 on the higher end, depending on factors such as location and experience. For instance, engineers in Palmdale, CA, have a median salary of $171,422, while those in St. Louis, MO, typically earn around $77,136.
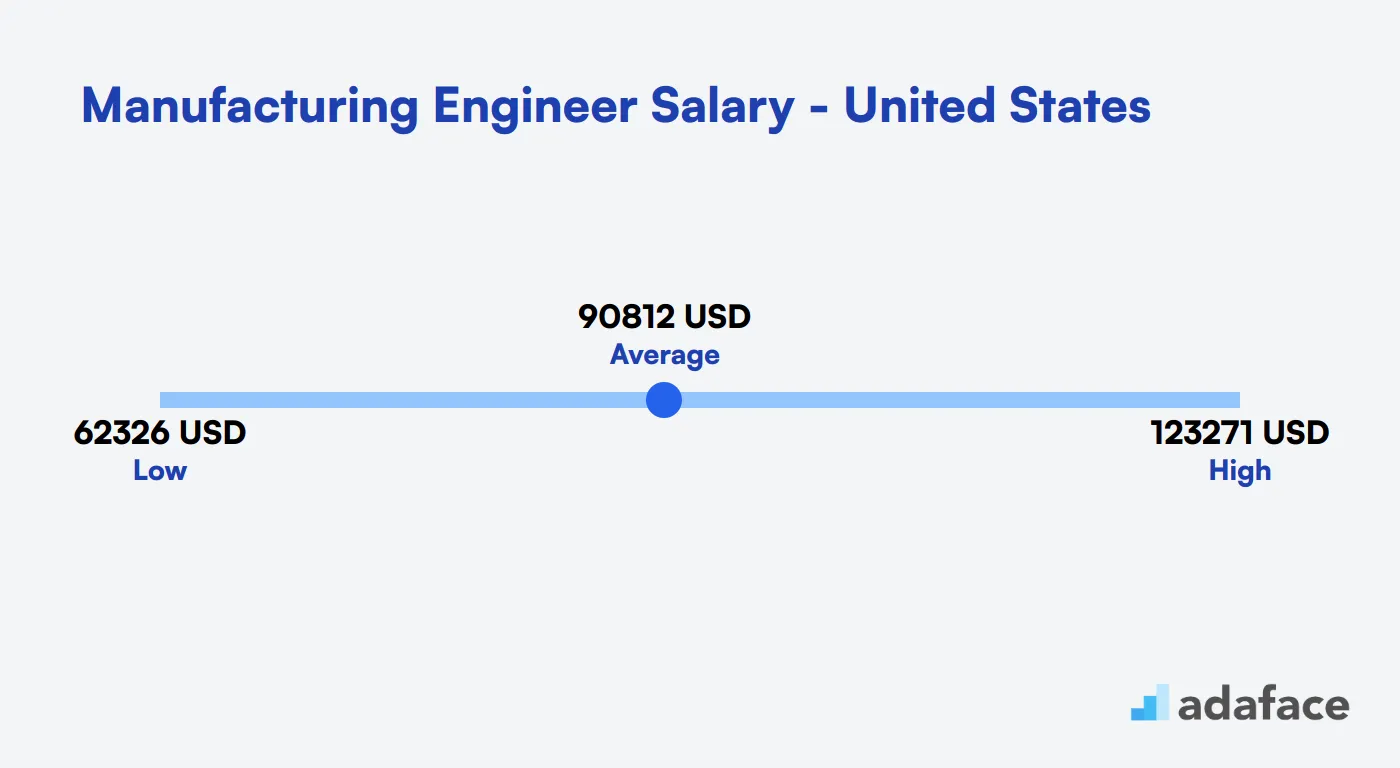
Manufacturing Engineer Salary in the United Kingdom
The average salary for Manufacturing Engineers in the United Kingdom ranges from £30,000 to £50,000 per year. Entry-level positions typically start around £25,000, while experienced professionals can earn up to £60,000 or more.
Factors influencing salary include location, industry, company size, and years of experience. Manufacturing Engineers in London and the South East often command higher salaries due to the higher cost of living in these areas.
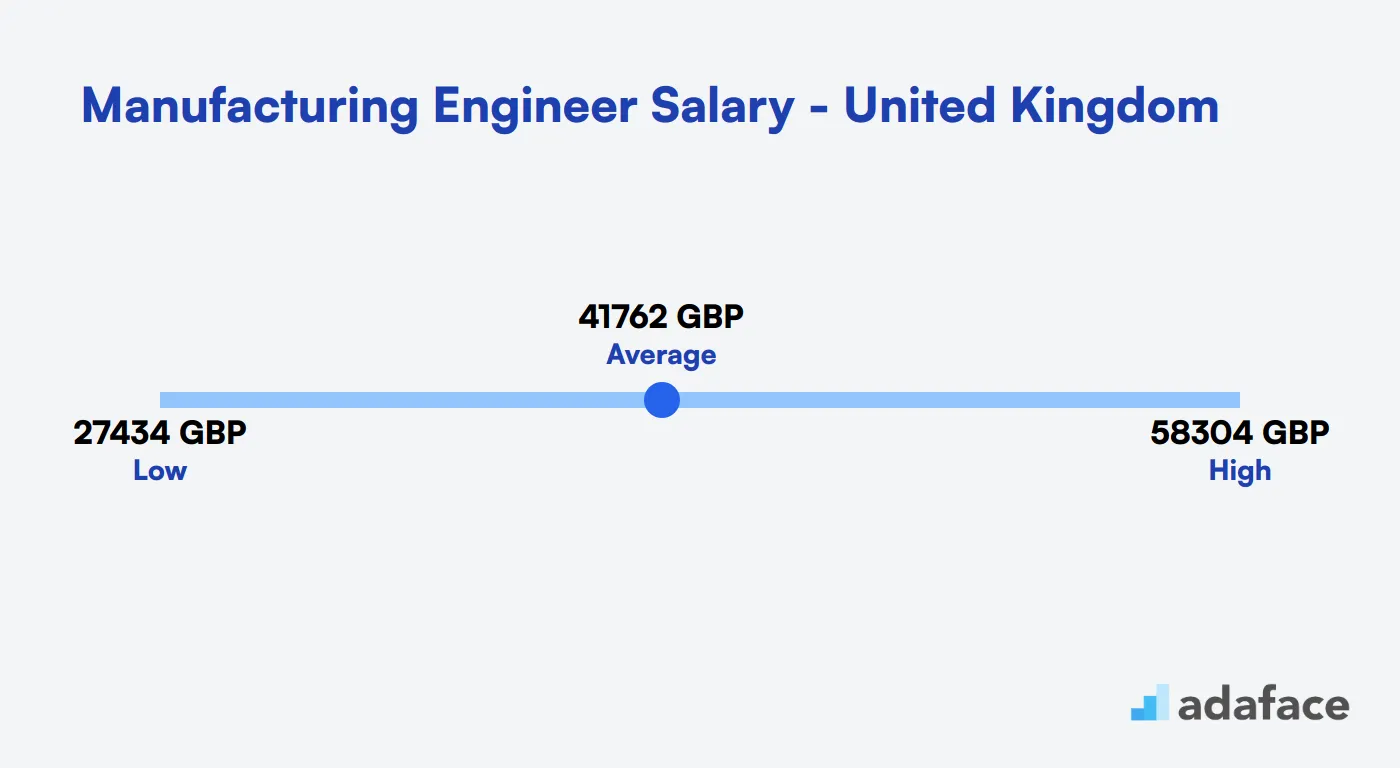
Manufacturing Engineer Salary in Australia
In Australia, the average salary for a Manufacturing Engineer is approximately AUD 109,340 per year. Salaries can vary significantly based on location, with Sydney offering the highest salaries, ranging from AUD 77,028 to AUD 139,384. Other major cities like Melbourne and Brisbane have averages around AUD 95,000 and AUD 98,000, respectively.
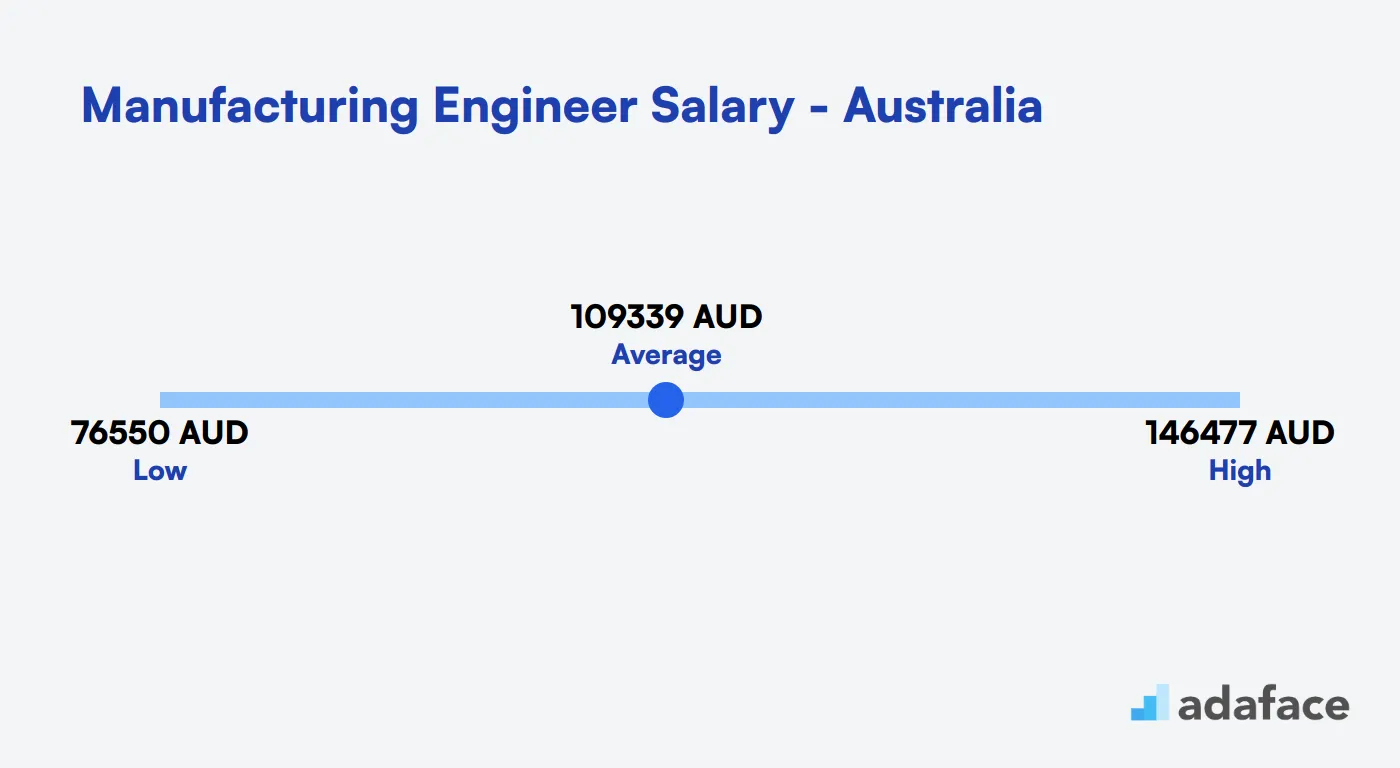
Manufacturing Engineer Salary in India
The average salary for a Manufacturing Engineer in India is approximately INR 556,509 per year. Salaries can range from around INR 213,541 at the lower end to INR 1,006,093 at the higher end. In cities like Bengaluru, the median salary is about INR 919,869, whereas in Chennai, it tends to be lower at INR 278,471.
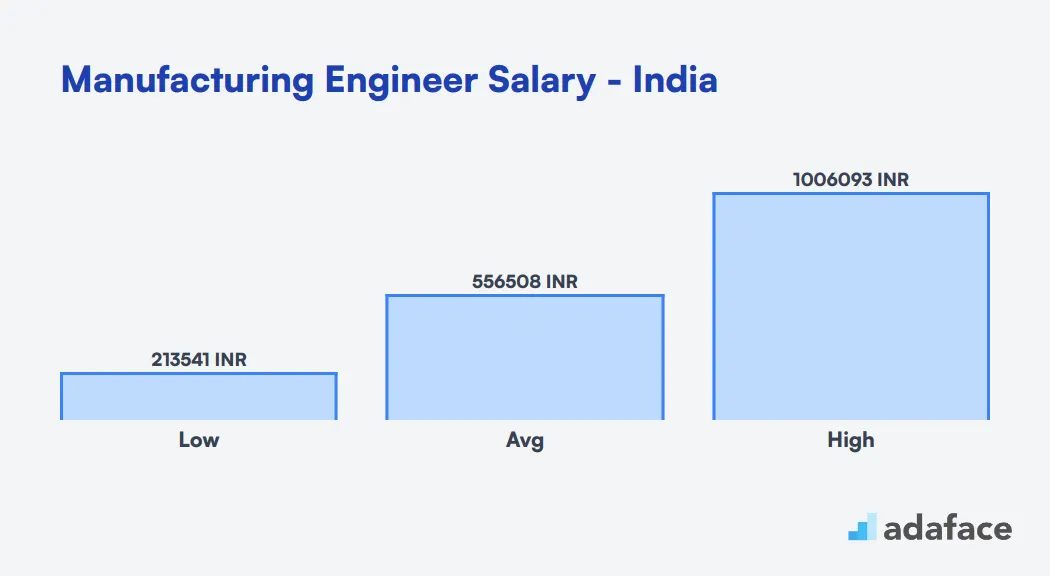
What's the difference between a Manufacturing Process Engineer and a Manufacturing Design Engineer?
Many people tend to confuse the roles of Manufacturing Process Engineer and Manufacturing Design Engineer due to their overlapping presence in the production environment. While both positions are integral to manufacturing, they focus on different aspects of the process.
A Manufacturing Process Engineer primarily concentrates on process optimization, aiming to improve production efficiency. They are experts in tools like process mapping software and often hold an industrial engineering degree, complemented by certifications like Lean Six Sigma. Their collaboration typically involves working closely with production teams to drive efficiency metrics.
In contrast, a Manufacturing Design Engineer is focused on product design and manufacturability. This role requires proficiency in CAD and simulation tools, often necessitating a degree in mechanical engineering. They collaborate with R&D teams to ensure that design specifications align with manufacturing capabilities.
Manufacturing Process Engineer | Manufacturing Design Engineer | |
---|---|---|
Focus Area | Process Optimization | Product Design |
Main Responsibilities | Improve production efficiency | Design products for manufacturability |
Key Skills | Lean Manufacturing, Six Sigma | CAD, Simulation Tools |
Typical Education | Industrial Engineering | Mechanical Engineering |
Collaboration | Works with production teams | Works with R&D teams |
Tools Used | Process Mapping Software | CAD Software |
Outcome Measurement | Efficiency Metrics | Design Specifications |
Certifications | Lean Six Sigma Certification | Certified SolidWorks Professional |
What are the ranks of Manufacturing Engineers?
The manufacturing engineering field often leads to confusion due to the varying titles and responsibilities associated with different ranks. Understanding these ranks can help recruiters find the right candidates with the specific skills needed for their organizations.
• Manufacturing Engineer I: This is an entry-level position where individuals typically assist with basic engineering tasks. They focus on learning the fundamentals of the manufacturing process and may work under the supervision of more experienced engineers.
• Manufacturing Engineer II: At this mid-level rank, engineers take on more responsibilities, including project management and process improvement initiatives. They are expected to have a deeper understanding of manufacturing systems and are often involved in troubleshooting production issues.
• Senior Manufacturing Engineer: Senior engineers lead projects and mentor junior staff. They possess extensive knowledge of manufacturing processes and are responsible for optimizing production efficiency, ensuring quality standards, and implementing innovative solutions.
• Lead Manufacturing Engineer: A lead engineer oversees a team of manufacturing engineers and coordinates engineering efforts across multiple projects. They are responsible for strategic planning and play a critical role in setting production goals.
• Engineering Manager: At the managerial level, this role involves overseeing the entire engineering department. Engineering managers are responsible for resource allocation, team development, and aligning engineering projects with organizational objectives.
• Director of Manufacturing Engineering: This top-tier position involves strategic leadership, setting long-term goals for the engineering department, and working closely with executive management. Directors are often key players in company-wide initiatives aimed at enhancing production capabilities.
Hire the Right Manufacturing Engineers for Your Team
Throughout this guide, we've explored the importance of manufacturing engineers, their roles, and the skills and qualifications necessary for success. We've also discussed the hiring process, from crafting an effective job description to conducting interviews. By now, you should have a solid understanding of how to approach hiring a manufacturing engineer.
If there's one key takeaway, it's that using detailed job descriptions and skill assessments can significantly enhance your hiring accuracy. Consider using tools like an attention to detail test or a technical aptitude test to ensure you're selecting the best candidates. These steps will help you build a strong and capable team.
Technical Aptitude Test
FAQs
A manufacturing engineer should typically have a bachelor's degree in engineering, along with experience in manufacturing processes, quality control, and production management.
Technical skills can be assessed through practical skills tests and problem-solving assessments. Consider using tools from our online assessment platform.
Candidates can be sourced from online job boards, professional networking sites, and industry-specific platforms. Our guide on top platforms to source manufacturing engineers can provide more insights.
Look for problem-solving skills, proficiency in manufacturing software, project management experience, and a strong understanding of production processes.
The interview process should include technical assessments, behavioral interviews, and discussions on past project experiences. Detailed guidance can be found in our section on structuring interview stages.
A Manufacturing Process Engineer focuses on optimizing production processes, while a Manufacturing Design Engineer is involved in product design and development. Both roles require different skill sets and expertise.
An effective job description should clearly state the role's responsibilities, required qualifications, and desired skills. Refer to our job description guide for detailed examples.
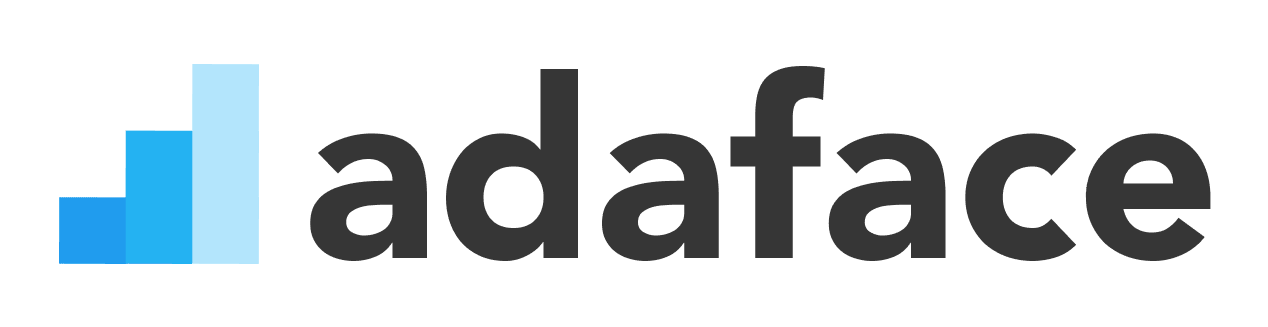
40 min skill tests.
No trick questions.
Accurate shortlisting.
We make it easy for you to find the best candidates in your pipeline with a 40 min skills test.
Try for freeRelated posts
Free resources
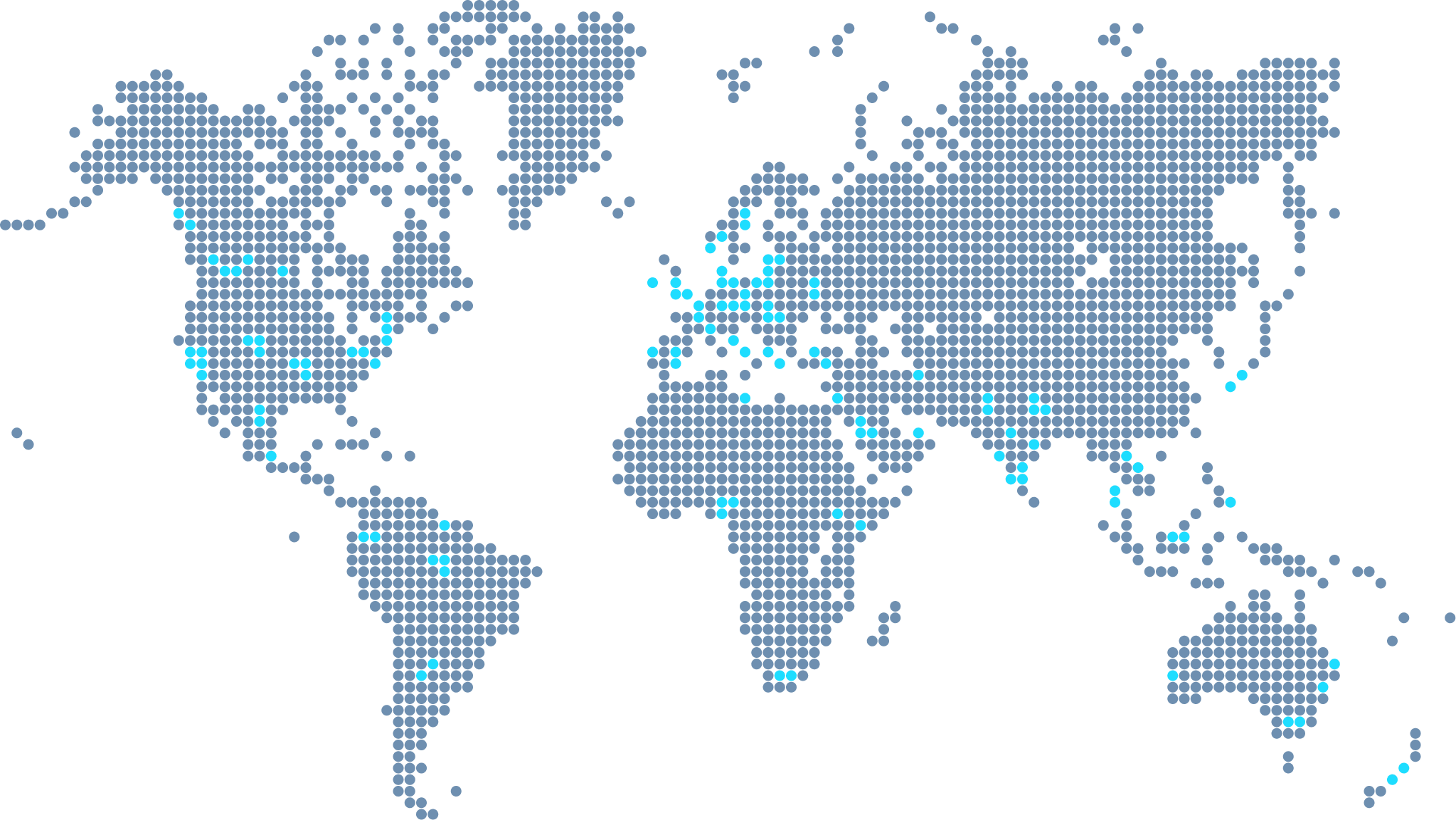
