When interviewing candidates for SAP MM roles, it's hard to find a go-to list of questions that will help you zero in on the best talent. You need targeted questions to sort through the noise and spot individuals with expertise; this becomes even more important when you need to hire SAP consultants with niche specializations.
This blog post provides a curated list of SAP MM interview questions tailored for various experience levels, from freshers to season professionals. This includes questions for freshers, juniors, intermediate and experienced professionals, and even some SAP MM MCQs.
By using these questions, you'll ensure you're evaluating candidates on the knowledge, and even better, you can use an SAP MM online test to screen candidates before the interview.
Table of contents
SAP MM interview questions for freshers
1. What is SAP MM, in simple terms? Can you give me a real-world example of how a company might use it?
SAP MM (Materials Management) is basically the SAP module that helps a company manage all the stuff it needs to buy, store, and use for its business. Think of it as the system that makes sure the company has the right materials, in the right quantities, at the right time, and at the right cost. It handles everything from creating purchase orders and receiving goods to managing inventory and paying vendors.
For example, imagine a manufacturing company that makes cars. They would use SAP MM to manage the procurement of all the parts needed to assemble a car - tires, seats, engines, etc. SAP MM helps them track inventory levels, automatically generate purchase orders when stock is low, receive and inspect incoming shipments, and pay suppliers. This ensures that they always have enough parts on hand to keep the assembly line running smoothly, without overspending on unnecessary inventory or facing production delays.
2. Imagine you are buying crayons for a school. How does SAP MM help you keep track of how many crayons you have, how much they cost, and when you need to buy more?
SAP MM (Materials Management) helps manage the crayon procurement process effectively. First, a material master record is created for crayons, storing information like description, unit of measure (e.g., box), and valuation. When purchase orders are created, SAP MM tracks the quantity ordered and the price per box. As crayons are received, goods receipts are entered, updating the inventory levels in SAP. This provides a real-time view of how many crayons are in stock.
SAP MM also helps with cost tracking. Invoice verification matches invoices against purchase orders and goods receipts, ensuring accurate pricing and recording the total cost of the crayons. To determine when to buy more, reorder points can be set in the material master. When the stock level falls below this point, SAP MM triggers a notification or automatically creates a purchase requisition, prompting a new order to be placed. Reports can also be generated to analyze crayon consumption and identify trends to improve purchasing decisions.
3. What's the difference between a material and a service in SAP MM, like explaining the difference between buying a toy and hiring a clown for a birthday party?
In SAP MM, a material is a tangible, physical good that can be stored, moved, and consumed. Think of buying a toy: you receive a physical object that you own, track in inventory, and eventually use up. Its value lies in its physical properties and inherent usefulness. The material is assigned to a material type and valuation class, making it easier to track its value in accounting.
A service, on the other hand, is an intangible activity or performance that provides value. Hiring a clown for a birthday party is a service: you're paying for the clown's time and entertainment, not a physical object. Services cannot be stored or inventoried; you receive the benefit at the time of performance. Instead of material master records, services are described through service master records or service specifications within purchase orders. The focus is on the description of the service and not its physical properties, as such accounting is handled differently from that of materials.
4. What is a purchase order, and why is it important? Pretend you're ordering pizza.
A purchase order (PO) is a document a buyer sends to a seller to authorize a purchase. It specifies the details of the order, such as the quantities, prices, and agreed-upon delivery date for the items or services being purchased. Think of it like this: I call the pizza place and say, "I want 2 pepperoni pizzas, large size, thin crust, for $20, deliver by 7 PM". The pizza place might create a PO internally to track my order and ensure they fulfill it correctly. They can reference this document and communicate using this common reference with other employees.
The importance of a PO lies in its ability to create a formal record of the transaction. It helps avoid misunderstandings and provides legal protection for both parties. It allows for better tracking and management of purchases. Using the pizza example, if the pizza arrives late and is incorrect, I can refer to the "PO" number from my order to resolve the issue more efficiently.
5. What does GR/IR mean, and what's its purpose?
GR/IR stands for Goods Receipt/Invoice Receipt. It's a clearing account used in accounting systems to temporarily hold the value of goods that have been received but not yet invoiced, or invoices that have been received but the goods haven't.
The purpose is to ensure accurate financial reporting by matching goods received with their corresponding invoices. It prevents discrepancies in accounts payable by providing a suspense account for items where either the goods or the invoice is pending, thereby facilitating reconciliation.
6. Can you explain what a 'vendor' is, in the context of SAP MM? Is it like a shopkeeper?
In SAP MM (Materials Management), a 'vendor' represents a supplier of goods or services to your organization. While you could think of them as similar to a shopkeeper in a very broad sense, the relationship is much more formal and structured. Vendors are business partners from whom you procure materials, services, or other resources necessary for your company's operations.
The vendor master record in SAP stores crucial information about each vendor, such as their address, payment terms, contact persons, and the materials or services they provide. This data is used throughout the procurement process, from creating purchase orders to processing invoices. It is more than just a shopkeeper relationship, it defines a business relationship and allows for purchasing and procurement activities in the SAP system.
7. What is the material master, and what kind of information does it hold? Think of it like a profile for each item.
The material master in systems like SAP is a central repository of information for all materials that a company purchases, manufactures, stocks, and sells. It's essentially a 'profile' for each material, holding all the relevant data needed to manage it throughout the supply chain.
The material master record contains information categorized into views, covering areas like:
- Basic Data: Material number, description, units of measure.
- Purchasing: Purchasing group, order unit, vendor information.
- Sales: Sales organization data, delivering plant.
- Accounting: Valuation class, price control.
- MRP (Material Requirements Planning): Planning strategy, safety stock.
- Storage: Storage location, warehouse management data.
- Quality Management: Inspection setup.
8. What does MRP do? How can it help make sure the shelves don't run empty?
MRP (Material Requirements Planning) is a planning and control system for inventory, production, and scheduling. It translates a master production schedule into requirements for components and raw materials, helping companies determine what materials are needed, how many are needed, and when they are needed to meet production demand.
MRP helps prevent empty shelves by ensuring timely availability of products. It achieves this by:
- Forecasting demand: MRP uses sales forecasts and historical data to predict future demand.
- Generating a production schedule: Based on demand forecasts and current inventory levels, MRP creates a production schedule.
- Creating a bill of materials (BOM): The BOM outlines the components and raw materials needed to produce each product.
- Calculating material requirements: MRP calculates the quantity of each material required based on the production schedule and the BOM.
- Planning procurement: MRP generates purchase orders for needed materials, ensuring they are ordered in time to meet production requirements. It also considers lead times for procurement.
- Inventory Control: By carefully planning and tracking material flow, MRP minimizes inventory holding costs and reduces the risk of stockouts.
9. What's the difference between a plant and a storage location in SAP MM? Are they both like boxes in a warehouse?
A plant and a storage location are both crucial organizational units in SAP MM, but they serve distinct purposes beyond simply being 'boxes in a warehouse'. A plant represents an operating area within a company, like a manufacturing facility, a distribution center, or a sales office. It's a logistical and organizational unit that can manufacture products, store materials, ship goods, perform service activities, and carry out planning. The plant is essential for valuation, inventory management, and production planning.
A storage location is a subdivision within a plant. It's a physical area where materials are stored. Think of it as a specific room or area within a plant's warehouse. Each plant can have multiple storage locations. Storage locations are primarily used for managing inventory quantities and differentiating stock within a plant. You can track stock at the storage location level. They provide granularity for inventory management within the overarching structure of the plant.
10. What is inventory management? Why is it important not to have too much or too little of something?
Inventory management is the process of ordering, storing, using, and selling a company's inventory. This includes managing raw materials, work-in-progress, and finished goods, as well as the associated warehousing and processing.
It's important to maintain optimal inventory levels. Too much inventory ties up capital, increases storage costs, and raises the risk of obsolescence or spoilage. Too little inventory can lead to stockouts, lost sales, production delays, and damage to customer relationships. Effective inventory management aims to balance these risks and optimize profitability.
11. Can you describe a goods receipt? What happens after the delivery truck arrives?
A goods receipt is the process of accepting delivery of goods into a warehouse or other designated location. When the delivery truck arrives, the process typically involves several steps:
First, the delivery is checked against the purchase order (PO) to verify the correct items and quantities are delivered. The goods are then inspected for damage or defects. Once verified, the goods receipt is recorded in the system (e.g., SAP, or a custom inventory management system), updating the inventory levels. This often involves creating a goods receipt document. Finally, the goods are moved to their designated storage location within the warehouse.
12. What's a purchase requisition? Is it like a shopping list?
A purchase requisition is an internal document used by employees to request the purchasing department to buy goods or services. It's more formal and detailed than a simple shopping list.
While a shopping list is an informal reminder of items to buy, a purchase requisition includes details like:
- Quantity
- Description of the item/service
- Vendor (if known)
- Price (estimated or quoted)
- Delivery date
- Account to be charged
- Approvals (from budget holders, etc.)
It's a formal request that initiates the purchase order process after the required approvals.
13. What's the purpose of a source list?
A source list, often referred to as a package list or repository list, serves as a configuration file for package management systems. Its primary purpose is to tell the package manager where to find software packages (applications, libraries, etc.) and their dependencies.
Specifically, it contains a list of URLs or file paths pointing to software repositories (often servers). The package manager uses this list to search for, download, and install software. Without a source list, the package manager wouldn't know where to retrieve packages from, and software installation would be impossible.
14. What are some of the key reports in SAP MM that you might use to see how much you're spending on materials?
Several SAP MM reports provide insights into material spending. Some key ones include:
- ME2N (Purchase Orders by PO Number): While not directly a spending report, it allows you to analyze POs, filter by material or vendor, and calculate total amounts spent within a specific timeframe. This helps in understanding spending patterns and identifying high-value materials or vendors.
- ME2L (Purchase Orders by Vendor): Displays purchase orders for a specific vendor. You can sum up the order values to see how much you've spent with a particular vendor.
- ME2M (Purchase Orders by Material): Shows purchase orders for a particular material. Analyzing this can show total spending on a particular material across different vendors.
- MB51 (Material Document List): This is useful for analyzing material movements. By filtering for goods receipts and correlating them with purchase orders, you can indirectly track material consumption and related spending.
- S_P00_07000139 (Purchasing Documents per Material Group): This report directly shows the spending per material group.
15. What do you understand about 'procurement cycle' in SAP MM? Take an example.
The procurement cycle in SAP MM (Material Management) refers to the entire process of acquiring materials or services, from initial identification of a need to the final payment to the vendor. It involves several key steps ensuring efficient sourcing and timely delivery of goods/services.
For example, consider a scenario where a company needs to procure office stationery. The cycle begins with a Purchase Requisition raised by the department needing the stationery. This requisition is then converted into a Purchase Order after approval. The PO is sent to the vendor. The vendor delivers the stationery, and a Goods Receipt is recorded in the system. After verification of the invoice against the PO and goods receipt, an Invoice Verification process is completed, and finally, the payment is made to the vendor, completing the procurement cycle. Key steps include: 1) Requirement Determination, 2) Source Determination, 3) Vendor Selection, 4) Purchase Order Processing, 5) Purchase Order Monitoring, 6) Goods Receipt, 7) Invoice Verification, 8) Payment Processing.
16. Have you heard about 'batch management' in SAP MM? What's the purpose?
Yes, I have heard about batch management in SAP MM. The purpose of batch management is to track and manage inventory of materials that have specific characteristics or attributes. It allows you to differentiate stock based on factors such as:
- Manufacturing date
- Origin
- Quality
- Expiration date
Batch management ensures that materials with different characteristics are handled separately and tracked throughout the supply chain, facilitating efficient inventory control, quality management, and recall management. Batches can have characteristics assigned to them, allowing for selection based on those characteristics during goods issue, transfer postings, and other inventory movements.
17. What are some of the benefits of using SAP MM?
SAP MM (Materials Management) offers several benefits. It streamlines procurement processes, ensuring timely availability of materials while optimizing costs. This is achieved through features like inventory management, purchase order processing, and invoice verification.
Key benefits include: Improved inventory control, Reduced procurement costs, Enhanced supply chain efficiency, Better vendor management, and Increased transparency in material flows.
18. Explain 'account determination' in SAP MM.
Account determination in SAP MM automatically determines the correct G/L accounts to be debited or credited during a transaction. This is crucial for financial accounting and ensures that all material movements and procurement processes are accurately reflected in the general ledger. It works based on a configuration that maps various transaction keys (e.g., BSX for inventory posting, WRX for GR/IR clearing) to specific G/L accounts, considering factors such as valuation class, material group, and plant.
19. What is a 'movement type' in SAP MM?
In SAP MM (Materials Management), a movement type is a three-character key that categorizes and differentiates stock movements. It determines how the quantity and value of materials are updated in the general ledger and material master records. Essentially, it defines the nature and purpose of a goods movement (e.g., goods receipt, goods issue, stock transfer). Each movement type is pre-configured with specific settings that control various aspects of the posting process, such as account determination and document creation.
Movement types are crucial for tracking inventory changes and ensuring accurate financial reporting. Examples include 101 for goods receipt for purchase order, 261 for goods issue for order, and 311 for stock transfer.
20. What is the use of 'info records' in SAP MM?
Info records in SAP MM (Material Management) serve as a bridge between materials and vendors. They store frequently used purchasing information for a specific material and vendor combination. This helps in streamlining the procurement process by automatically populating purchase orders and other purchasing documents with pre-negotiated pricing, delivery times, vendor details, and other relevant information. This reduces manual data entry and ensures consistency across purchase orders.
Specifically, info records maintain the following information:
- Current and future prices
- Delivery times
- Vendor data
- Last purchase order number
- Conditions and Texts.
21. How does SAP MM integrate with other modules like SAP FI? Can you give an example?
SAP MM (Materials Management) integrates with other modules, notably SAP FI (Financial Accounting), to ensure seamless financial postings related to material movements. When goods are received (GR) in MM, an accounting document is automatically created in FI. This document reflects the increase in inventory value and a corresponding credit to the GR/IR (Goods Receipt/Invoice Receipt) clearing account. This automatic posting ensures that the financial statements accurately reflect the company's inventory position.
For example, consider a purchase order for 100 units of a material at $10 per unit. Upon goods receipt, MM triggers an accounting document in FI. This document debits the inventory account by $1000 (100 units * $10) and credits the GR/IR clearing account by $1000. Later, when the invoice is received and processed, the GR/IR account is debited, and the vendor account is credited.
22. What do you know about 'special procurement types' in SAP MM?
Special procurement types in SAP MM define specific processes for acquiring materials that deviate from the standard purchase order process. They allow materials to be sourced in different ways, or from different locations, than the standard route. Some common examples include:
- Consignment: The vendor provides materials which are stored at your location, but you only pay for them when you use or consume them.
- Subcontracting: You send raw materials to a vendor, who then manufactures the finished product. You pay the vendor for their services. This is useful when a vendor has specific expertise or specialized equipment.
- Stock Transfer: Materials are moved between different plants within your company. This can be a stock transfer order (STO) which involves shipping or a direct transfer posting.
- Third-Party Order Processing: Sales order triggers a purchase requisition, that creates a purchase order to vendor and ships the product to the customer directly.
- Pipeline: Material is delivered from a pipeline (e.g., oil, gas) directly into your plant and is available for immediate consumption. Payment is based on usage.
23. How would you define 'valuation' in SAP MM, in simple terms?
In SAP MM, valuation refers to the method used to determine the monetary value of materials in your inventory. It essentially answers the question: 'What is the value of this material stock we have?'. This value is crucial for financial accounting, inventory management, and cost accounting purposes.
Valuation involves assigning a price to the material, which could be based on several methods such as standard price, moving average price, or FIFO (First-In, First-Out). The chosen valuation method impacts how the material's value is recorded in the general ledger and how cost of goods sold is calculated when the material is consumed or sold.
24. What is the use of release strategy in purchasing documents?
Release strategies in purchasing documents (like purchase requisitions and purchase orders) implement an approval workflow. They ensure that purchasing decisions above a certain monetary value or meeting specific criteria (e.g., material group, plant) require authorization from designated personnel. This provides better control over spending and compliance with company policies.
Specifically, release strategies:
- Control the creation of POs. A PO cannot be sent to the vendor without proper release.
- Enforce spending limits, preventing unauthorized purchases exceeding budget.
- Ensure compliance with internal guidelines.
- Provide an audit trail of approvals.
- Often tied to specific user roles (e.g., manager, department head, financial controller). The document will loop through each person who has authorization to release.
25. What are some common challenges companies face when implementing SAP MM?
Implementing SAP MM (Material Management) can present several challenges. Data migration is often a significant hurdle, ensuring data accuracy and completeness when transferring from legacy systems. User adoption can also be challenging, requiring effective training and change management to ensure users understand and utilize the new system properly. Configuration complexity is another common issue, correctly configuring the system to align with specific business processes, requiring deep expertise.
Other challenges include integration with other SAP modules (like FI, SD, PP), which demands careful planning and testing, and maintaining data quality over time, which requires establishing robust data governance policies. Customization can also lead to complications, as excessive modifications can increase complexity and make future upgrades more difficult. Finally, ensuring proper security roles and authorizations is vital to prevent unauthorized access to sensitive data.
26. Explain 'invoice verification' in SAP MM. What happens when the invoice arrives?
Invoice verification in SAP MM (Materials Management) is the process of checking the accuracy of an invoice received from a vendor against the purchase order and goods receipt. When an invoice arrives, several things happen. First, the system checks if a corresponding purchase order exists. Then, it verifies the quantities, prices, and terms against the purchase order and goods receipt (if applicable). Discrepancies, such as price or quantity differences, trigger a blocking mechanism, preventing payment until the issue is resolved.
Invoice verification can be done manually or automatically. Manual invoice verification involves manually entering the invoice details into the system and reviewing any discrepancies. Automatic invoice verification relies on predefined tolerance limits and matching rules to automatically process invoices that fall within acceptable ranges. Once the invoice is verified and approved, the system posts the invoice to accounts payable, updating the relevant financial records.
SAP MM interview questions for juniors
1. What is SAP MM, in simple words, like explaining it to a kid?
Imagine you're helping your parents manage the house. SAP MM is like a super organized system that helps companies keep track of all the stuff they need to buy and use – like ingredients for a restaurant, parts for a car factory, or even office supplies. It makes sure they always have the right amount of things, don't run out, and don't waste money by buying too much.
Basically, SAP MM helps companies manage their shopping and storage, ensuring they have everything they need to make their products or provide their services efficiently. It's all about planning, buying, storing and managing materials.
2. Imagine you are ordering toys for all your friends. How does SAP MM help a company order lots of things it needs?
SAP MM (Materials Management) helps companies order lots of things by streamlining the entire procurement process. It manages everything from creating purchase requisitions to receiving goods and paying vendors. It ensures that the right materials are available at the right time and in the right quantity, preventing stockouts or overstocking.
Specifically, SAP MM supports ordering by providing features like: automatic purchase order creation based on defined reorder points, vendor selection based on price and delivery time, goods receipt processing to accurately track incoming materials, and invoice verification to ensure accurate payment to vendors. These features are all integrated, providing a central view of all procurement-related activities.
3. What are the different types of materials that a company might need to buy using SAP MM?
SAP MM handles procurement of various material types. These broadly fall into: Raw Materials (used directly in production), such as steel, chemicals, or fabrics; Semi-Finished Goods (partially processed items), like sub-assemblies or components; Finished Goods (ready-to-sell products); Trading Goods (items bought and sold without further processing); Operating Supplies (MRO - Maintenance, Repair, and Operations), including lubricants, cleaning supplies, and spare parts; Consumable Materials (used in day-to-day operations), such as office supplies; and Services (externally provided activities) like consulting or maintenance services. Each material type is configured differently in SAP MM to manage its specific procurement process and inventory management requirements.
These different categories are managed using material types within SAP, which control aspects such as account determination, inventory management, and purchasing behavior. The material type determines how a material is treated within the SAP system.
4. Can you name some important documents used in SAP MM when a company wants to buy something?
In SAP MM, several important documents are used throughout the procurement process. These documents facilitate tracking, approval, and execution of the purchasing cycle. Some key documents include:
- Purchase Requisition: An internal document requesting the purchasing department to procure materials or services. It can be created manually or automatically (e.g., by MRP).
- Purchase Order: A formal document sent to a vendor to order goods or services. It specifies details like quantity, price, delivery date, and terms.
- Quotation: A document received from a vendor in response to a request for quotation (RFQ), outlining the vendor's price and terms for supplying the requested goods or services.
- Goods Receipt: A document used to record the receipt of goods from a vendor. It updates inventory and triggers accounting entries.
- Invoice Receipt: A document used to verify and record vendor invoices. It is matched against the purchase order and goods receipt to ensure accuracy before payment.
5. What is a purchase order in SAP MM, and what important information does it contain?
In SAP MM (Materials Management), a purchase order (PO) is a formal document issued by a buyer to a seller, indicating the buyer's intention to purchase specific goods or services. It's a legally binding agreement once accepted by the supplier. It initiates the procurement process.
Key information contained in a purchase order includes: vendor details (name, address), material/service description, quantity, price, delivery date, payment terms, purchase order number (unique identifier), currency, incoterms, and plant/storage location where goods should be delivered. It may also contain conditions of purchase, such as penalties for late deliveries.
6. What is a goods receipt in SAP MM, and why is it important to record it?
A goods receipt in SAP MM (Materials Management) is the process of accepting delivery of goods into the company's inventory. It's essentially a record that confirms the physical arrival of materials ordered from a vendor or produced internally. When a goods receipt is posted, the system updates the inventory quantities and values accordingly.
Recording goods receipts is important for several reasons. Primarily, it ensures accurate inventory management, allowing the company to track stock levels and avoid shortages or overstocking. It also triggers financial postings, updating the general ledger with the value of the received goods, and provides a basis for invoice verification, matching the received quantity against the vendor's invoice for payment. Without accurate goods receipts, the entire procurement and financial processes can be flawed, leading to incorrect inventory valuation and potential payment discrepancies.
7. What is invoice verification in SAP MM, and why is it important to match it with the purchase order and goods receipt?
Invoice verification in SAP MM (Materials Management) is the process of checking invoices received from vendors against the purchase order (PO) and goods receipt (GR) to ensure accuracy and validity before payment. It's a crucial step in the Procure-to-Pay cycle.
Matching the invoice with the PO and GR is important for several reasons:
- Preventing overpayment: Ensures you only pay for what you ordered and received.
- Detecting discrepancies: Identifies any differences in quantity, price, or terms.
- Ensuring accuracy: Validates that the invoice is correct and complies with the agreed-upon terms.
- Streamlining payments: Facilitates timely and accurate payments to vendors.
- Maintaining accurate inventory: Helps reconcile inventory records with payments.
- Avoiding fraud: Reduces the risk of paying fraudulent invoices.
8. What is a material master in SAP MM, and what kind of information does it store about a material?
In SAP MM (Materials Management), a material master is a central repository of information about all the materials that a company procures, produces, stores, and sells. It serves as a single source of truth for material-related data across the entire organization.
The material master stores various types of information, including:
- Basic Data: Material number, description, unit of measure, material group.
- Purchasing Data: Purchasing group, ordering unit, vendor information.
- Sales Data: Sales organization, distribution channel, delivering plant.
- MRP Data: Planning strategy, safety stock, reorder point.
- Accounting Data: Valuation class, price control, standard price.
- Storage Data: Storage location, storage bin, handling unit.
- Classification Data: Characteristics and values for material classification.
9. What is a vendor master in SAP MM, and what kind of information does it store about a supplier?
In SAP MM (Materials Management), a vendor master is a central repository of information about a company's suppliers. It stores all the data needed to conduct business with a vendor, ensuring consistent and accurate information across the organization.
The vendor master stores a wide range of information, including:
- General Data: Name, address, contact details, language, search terms.
- Company Code Data: Reconciliation account, terms of payment, payment methods, dunning procedure.
- Purchasing Organization Data: Purchasing group, currency, incoterms, order acknowledgement requirements, partner schema.
10. What is a purchase requisition in SAP MM, and who usually creates it?
A purchase requisition in SAP MM (Materials Management) is an internal document used to request the purchasing department to procure specific goods or services. It's essentially an internal request indicating a need for something. It doesn't commit the company to a purchase, but it's the starting point for the procurement process.
Typically, a purchase requisition is created by an employee or department that needs the goods or services. This could be someone from production, maintenance, or any department that requires materials for their operations. The creator doesn't need purchasing authority; they simply need to identify the requirement.
11. What are some of the key benefits of using SAP MM for a company's procurement process?
SAP MM (Materials Management) offers several key benefits for a company's procurement process. Improved efficiency and automation are central, streamlining processes from requisition to payment. It enhances inventory management, optimizing stock levels and reducing carrying costs. SAP MM facilitates better supplier relationship management, enabling negotiation of favorable terms and improved collaboration.
Furthermore, it strengthens compliance and control through defined workflows and approval processes. Cost savings are realized through optimized purchasing, reduced inventory, and improved supplier performance. Real-time visibility into the entire procurement lifecycle allows for informed decision-making and proactive issue resolution. The system facilitates proper document keeping which further facilitates auditing.
12. What is meant by 'source of supply' in SAP MM, and how does it help in procurement?
In SAP MM (Materials Management), 'source of supply' refers to the origin from which a material is procured. This could be an internal source (e.g., production within the company) or an external source (e.g., a vendor). It essentially defines where the material is coming from.
The source of supply helps in procurement by streamlining the purchasing process. It allows the system to automatically determine the appropriate vendor or source for a material based on factors like price, delivery time, or existing agreements (e.g., contracts or scheduling agreements). This automation reduces manual effort, improves efficiency, and ensures that materials are procured from the most advantageous source, leading to cost savings and optimized supply chain management.
13. Explain the concept of 'batch management' in SAP MM, and why is it used?
Batch management in SAP MM allows you to track and manage materials with similar characteristics throughout their lifecycle. A batch is a specific quantity of material that is produced or received at a specific time and shares common properties (e.g., color, size, potency, manufacturing date). These characteristics are defined in batch master records.
Batch management is used for several key reasons:
- Traceability: Enables you to trace materials back to their origin (e.g., manufacturer, production date). This is crucial for quality control and recall management.
- Quality Control: Allows you to track the quality of individual batches and manage their usage accordingly. For example, you can restrict the use of a batch that fails a quality test.
- Inventory Management: Provides more granular control over inventory by differentiating materials with the same material number but different characteristics.
- Shelf Life Management: Helps manage materials with expiration dates by tracking the remaining shelf life of each batch.
- Regulatory Compliance: Required for certain industries (e.g., pharmaceuticals, food) to comply with regulations regarding traceability and quality control.
14. What is a 'valuation class' in SAP MM, and how does it relate to accounting?
A valuation class in SAP MM (Materials Management) is a key configuration setting that determines the General Ledger (G/L) accounts to which material movements (goods receipts, goods issues, etc.) are posted. It acts as a bridge between the material master record and the financial accounting system. Essentially, it groups materials with similar accounting characteristics.
When a material movement occurs, the system uses the valuation class assigned to that material in its material master, along with other factors such as the transaction type, to determine which G/L accounts should be debited and credited. This ensures that inventory values and material consumption are accurately reflected in the financial statements. Without valuation classes, you'd have to manually determine the accounting impact of each material transaction, making the process much more cumbersome and prone to errors.
15. What is 'MRP' in SAP MM, and what does it help with?
MRP in SAP MM stands for Material Requirements Planning. It's a planning and control system used to manage inventory and ensure that materials are available when needed for production or sales.
MRP helps with several key tasks, including determining the quantity and timing of material requirements, generating purchase requisitions and production orders, optimizing inventory levels, and avoiding stockouts or excess inventory. It uses demand forecasts, bill of materials, and inventory data to calculate the necessary materials and schedule their procurement or production.
16. Can you explain what a 'storage location' is in SAP MM?
In SAP MM (Materials Management), a storage location is a subdivision of a plant where materials are physically stored. It's a crucial element for managing inventory at a granular level. Think of it as a specific area within a plant, like a warehouse section or a designated shelf.
Storage locations allow you to differentiate between quantities of the same material stored in different physical locations within the same plant. This provides better tracking and control over inventory, enabling more accurate stock management and reporting. Different business processes can be configured at storage location level, such as stock determination or putaway strategies.
17. What is the difference between 'stock material' and 'non-stock material' in SAP MM?
In SAP MM (Materials Management), the key difference between stock and non-stock materials lies in how they are managed in inventory. Stock materials are tracked quantitatively. SAP manages the quantity and value of these materials; goods receipts are posted to inventory, consumption is tracked, and physical inventory counts are performed. They have a material master record containing accounting and inventory management data.
Non-stock materials, on the other hand, are not typically stored in inventory and are directly consumed. There is often no quantity tracking. Purchases are generally expensed directly to a cost center or order. While a material master record can exist, it might only contain basic information (description, material group). Inventory management data is generally absent or irrelevant because SAP doesn't track the quantity on hand. Examples include office supplies purchased for immediate use.
18. Describe the 'procurement cycle' in SAP MM in simple steps.
The procurement cycle in SAP MM (Materials Management) outlines the steps involved in acquiring materials or services. It typically starts with determining the need - this could be through MRP (Material Requirements Planning) or a manual request. Then a Purchase Requisition is created either automatically by MRP or manually by a user. Next, source determination occurs, identifying potential vendors. A Purchase Order (PO) is created and sent to the selected vendor. Once the goods or services are received, a Goods Receipt (GR) is posted, updating inventory. Finally, an Invoice Verification is performed to match the invoice with the PO and GR, and then the invoice is paid.
In essence, the process flows from identifying a need, creating a purchase request, sourcing the material, creating a purchase order, receiving goods or services, performing invoice verification, and then paying the vendor. Each step involves specific SAP transactions and processes to ensure proper control and documentation.
19. What is a 'three-way match' in SAP MM, and why is it important for invoice processing?
A three-way match in SAP MM is a process of verifying the accuracy and consistency between three key documents before an invoice is paid. These documents are: the purchase order (PO), the goods receipt (GR), and the invoice. It's important because it ensures that the company only pays for goods that were actually ordered, received, and invoiced at the correct price and quantity. This helps prevent fraudulent payments and discrepancies, thereby improving financial control and accuracy in accounts payable.
The process involves matching the data on each of the three documents. For example, the quantity ordered on the PO should match the quantity received on the GR, and both should match the quantity invoiced. Similarly, the price per unit on all three documents should align. Any discrepancies identified during the three-way match process will flag the invoice for further investigation and resolution, potentially preventing incorrect payments.
20. What are some common reports that you might use in SAP MM, and what information do they provide?
Some common reports in SAP MM include: Inventory Management Reports (e.g., MB52 - Display Warehouse Stocks) which show current stock levels of materials. Purchasing Reports such as ME2N (Purchase Orders by PO Number) provide information on purchase order status, quantities, and values. Consumption Reports (e.g., MC.9 - Material Consumption Analysis) helps analyze material usage over time. These reports provide crucial insights into stock levels, procurement activities, and consumption patterns.
Specifically, the MB52 report displays stock information across various storage locations and organizational levels. ME2N provides details about POs based on different selection criteria like PO number, material, or vendor. MC.9 report is useful for identifying trends and planning future material requirements. In addition to these, transaction code MMBE
provides a consolidated stock overview for a material across different plants and storage locations.
21. How do you think SAP MM helps a company save money?
SAP MM (Materials Management) helps companies save money in several ways. By efficiently managing the procurement process, MM minimizes waste and optimizes inventory levels. This reduces storage costs and the risk of obsolescence. Accurate demand forecasting and material planning, facilitated by MM, prevent stockouts and overstocking, leading to cost savings.
Furthermore, SAP MM streamlines supplier relationships and negotiations. Centralized procurement processes and data-driven insights enable companies to negotiate better prices and payment terms with suppliers. MM also automates tasks like invoice verification, reducing manual effort and errors, which ultimately contribute to cost savings and improved efficiency.
22. What is a 'movement type' in SAP MM, and give an example?
In SAP MM (Materials Management), a movement type is a three-digit key that classifies and differentiates various types of stock movements. It determines how the stock quantity and value are updated in the system. Each movement type has predefined settings that control the accounting postings, stock updates, and other processes triggered by the goods movement.
For example, movement type 101 is commonly used for a goods receipt for a purchase order. This movement type increases the stock quantity and value in the warehouse. Other examples include 311 (stock transfer posting), 261 (goods issue for production order), and 561 (initial entry of stock balances).
23. What is 'physical inventory' in SAP MM and why do companies do it?
Physical inventory in SAP MM refers to the process of physically counting the stock in a warehouse or storage location and comparing it with the system records (SAP inventory data). It's essentially a stocktaking exercise to verify the accuracy of the inventory data in SAP.
Companies conduct physical inventory for several reasons:
- Accuracy: To ensure that the actual stock matches the recorded stock, which is crucial for planning, procurement, and sales.
- Compliance: Meeting regulatory requirements and audit needs.
- Discrepancy Identification: Uncovering discrepancies caused by errors, theft, damage, or obsolescence. It helps to determine the root cause and to take corrective actions.
- Financial Reporting: Providing accurate inventory valuation for financial statements.
- Optimizing Inventory Management: Helps to identify slow-moving or obsolete items to improve inventory turnover and reduce holding costs.
24. Imagine a company needs to return damaged goods. How would SAP MM help with that?
SAP MM (Materials Management) provides several functionalities to handle the return of damaged goods. The process typically starts with creating a return purchase order, referencing the original purchase order. This allows you to track the return against the initial procurement. You can also use return delivery in conjunction with the purchase order and material document.
SAP MM facilitates the inspection of returned goods. Based on the inspection results (accepted or rejected), you can trigger subsequent processes such as credit memo processing (if accepted), or scrapping (if rejected). Quantity updates for the returned material are also managed within MM, ensuring accurate inventory records. Material movements and stock postings are automatically updated with movement type 161, 162 etc.
25. What is a 'service entry sheet' in SAP MM, and when is it used?
A service entry sheet (SES) in SAP MM is a document used to formally accept and record the completion of services performed by a vendor. It acts as a confirmation that the services ordered have been delivered according to the purchase order.
Service entry sheets are typically used when procuring services, such as maintenance, repairs, or consulting. After a vendor performs the services, a service entry sheet is created to document the details of the work completed. Once the service entry sheet is approved, it triggers the payment process to the vendor. SES are used in conjunction with service purchase orders.
26. In your own words, what is the most important thing you learned about SAP MM?
The most important thing I learned about SAP MM is the critical role of accurate and timely data management in ensuring efficient procurement and inventory management. Understanding how master data (material master, vendor master, purchasing info records) drives the entire process, from purchase requisition to invoice verification, is key. Without accurate and consistent master data, the entire supply chain can be disrupted, leading to delays, errors, and increased costs.
Furthermore, I realized the significance of integration between MM and other SAP modules like FI/CO and SD. This integration allows for seamless flow of information across different business functions, enabling better decision-making and improved overall business performance. Understanding these dependencies helps to appreciate the holistic nature of SAP and its impact on the organization.
SAP MM intermediate interview questions
1. Can you explain the difference between a purchase requisition and a purchase order in SAP MM, and how they relate to each other? Imagine explaining it to someone who has never used SAP before.
Imagine your company needs to buy something. A purchase requisition is like an internal request form. It's created by an employee to tell the purchasing department what they need, how much, and when they need it. It's essentially an internal document asking for permission to buy something. The purchasing department then reviews the requisition. If approved, it gets converted into a purchase order.
A purchase order (PO) is a formal document sent to an external vendor (supplier) to actually order the goods or services. It commits the company to buying those items, and includes details like price, quantity, delivery date, and payment terms. So, the requisition is the request, and the purchase order is the actual order sent to the supplier. The PO references the requisition, creating a link in the system.
2. What are the key steps in the procurement cycle within SAP MM, from requirement identification to invoice verification? Keep it simple!
The SAP MM procurement cycle involves several key steps. First, Requirement Identification determines the need for materials or services. Next, a Purchase Requisition is created, either manually or automatically. This is followed by Source Determination, where potential suppliers are identified. A Purchase Order (PO) is then created and sent to the selected vendor. After that, Goods Receipt (GR) occurs when the materials are received and verified against the PO. Finally, Invoice Verification processes the vendor invoice, matching it against the PO and GR before payment is made.
In summary, the cycle flows like this: Requirement -> Requisition -> Source -> PO -> Goods Receipt -> Invoice Verification.
3. Describe the different types of special procurement keys in SAP MM and when you would use each one. Make it so a child can understand.
Imagine you're getting toys! Sometimes, instead of buying a toy directly, you ask someone else to make it or you borrow it from a friend. SAP's special procurement keys are like labels telling the computer how you're getting the materials (like parts for making toys) instead of just buying them normally.
Here are a few types explained simply:
- Consignment: It's like borrowing a toy! The store lets you have the toy, and you only pay if you use it. In SAP, the vendor provides materials, but you only pay when you use them.
- Subcontracting: You're asking someone else to make a toy for you. You give them the parts, and they assemble it. In SAP, you provide components to a vendor who then assembles the final product.
- Stock Transfer: Getting a toy from another playroom! You move materials from one plant (like a warehouse) to another within your company. No real purchasing involved, just moving stock.
- External processing: Sending a toy outside for a paint job! A vendor performs specific operations on our manufactured parts. For example, heat treatment or painting.
4. How do you configure automatic account assignment in SAP MM, and why is it important for financial accounting? Make it simple.
Automatic account assignment in SAP MM (Materials Management) links procurement activities to the correct General Ledger (G/L) accounts in Financial Accounting (FI) automatically. It's configured primarily through transaction OMWB
(Valuation Grouping Code), OBYC
(Transaction Key configuration), and material master settings. You define valuation grouping codes (grouping plants for valuation purposes), transaction keys (like BSX for inventory posting or WRX for GR/IR clearing), and G/L accounts for each combination. When a goods movement occurs, SAP uses these settings to determine the appropriate G/L account to post to based on material, plant, and transaction type.
It's important because it ensures accurate and consistent financial reporting. Without it, manual account assignment would be required for each transaction, increasing the risk of errors and delays. Automatic account assignment guarantees that inventory values, consumption, and other procurement-related costs are correctly reflected in the financial statements, enabling proper financial analysis and control.
5. What is a source list in SAP MM, and how does it help in the procurement process? Like explaining it to a 5 year old!
Imagine you want to buy your favorite toy. A source list in SAP is like a list of all the stores where you can buy that toy. It tells the system (like a helpful grown-up) where it can get the things the company needs. It's a list of approved vendors/suppliers.
It helps the procurement process because:
- It makes sure you always buy from the right stores (approved suppliers).
- It helps you find the best price. If one store is too expensive, you can check the others on the list.
- It can automatically choose the best store for you, making buying things faster and easier.
6. Explain the concept of quota arrangement in SAP MM and how it's used to distribute orders among different vendors. Simple please!
Quota arrangement in SAP MM is a way to automatically distribute purchase orders among different vendors for a specific material. It ensures that no single vendor is overloaded while others are idle. It's based on a quota which is a percentage assigned to each vendor.
How it works: When a purchase requisition or order is created, SAP checks the quota arrangement. Based on the quota percentage assigned to each vendor, SAP automatically determines which vendor should receive the order. It can also be configured based on historical data such as past order quantities or delivery performance, allowing for optimal vendor selection.
7. How does SAP MM handle subcontracting processes, and what are the key master data and transactions involved? Simple explaination.
SAP MM handles subcontracting by sending raw materials to a vendor (subcontractor), who then manufactures the finished product. The vendor is paid for their services, and the finished product is received back into inventory.
Key master data includes: Material Master (for raw materials and finished goods), Vendor Master, and Bill of Materials (BOM). Key transactions include: ME21N (creating a subcontracting purchase order), ME2O (monitoring stock provided to vendor), MIGO (goods receipt of the finished product), and MIRO (invoice verification for the vendor's services).
8. What are the different types of inventory management movement types in SAP MM, and provide examples of when each would be used?
SAP MM (Materials Management) uses movement types to categorize and track inventory changes. These types determine how inventory quantities and values are updated in the system. Some common movement types include:
- 101 (Goods Receipt for Purchase Order): Used when receiving goods from a vendor against a purchase order. This increases the stock quantity.
- 102 (Goods Receipt for Purchase Order - Reversal): Reverses a 101 movement, effectively undoing the receipt.
- 201 (Goods Issue for Cost Center): Used when issuing materials for consumption in a cost center (e.g., office supplies). This decreases the stock quantity.
- 261 (Goods Issue for Production Order): Issues materials to a production order for manufacturing. This reduces stock, and creates a record of materials used in production.
- 311 (Stock Transfer Posting): Transfers stock from one storage location to another within the same plant.
- 301 (Stock Transfer Posting - Plant to Plant): Transfers stock from one plant to another.
- 561 (Initial Entry of Stock): Used to enter initial stock balances into the system during implementation or when taking over stock. This adds inventory to stock without a preceding goods receipt. It can also be used during inventory counts where the physical stock on hand is higher than the book inventory.
- 601 (Goods Issue for Delivery): Used when issuing materials for a customer delivery. This reduces the stock quantity available for future orders. Typically used with Sales and Distribution SD module.
- 701/702 (Inventory Differences): These are used to adjust book inventory to match physical inventory after a count. 701 is for increasing stock and 702 is for decreasing stock.
These movement types are essential for maintaining accurate inventory records and enabling proper material planning and costing in SAP.
9. Describe the process of physical inventory counting in SAP MM and how discrepancies are handled. Make it so a child understands.
Imagine you have a big box of LEGO bricks in SAP MM. Physical inventory counting is like checking how many LEGO bricks you actually have in the box compared to what the computer thinks you have. We go to the box and count each LEGO brick carefully. Then, we write down the real number. If the real number is different from the number in the computer, that's a discrepancy!
To fix discrepancies, we tell the computer about the real number of LEGO bricks. SAP will then change the number in the system to match the real count. We investigate why the numbers were different. Maybe someone used some LEGO bricks without telling the computer, or perhaps some LEGO bricks were damaged and thrown away. After understanding why it happened, we can fix the process to avoid such differences in the future, like reminding people to tell the computer when they use or remove LEGO bricks!
10. What are the key functionalities of the MRP (Material Requirements Planning) module in SAP MM? Simplify it!
The MRP module in SAP MM is like a planning assistant that helps ensure you have the right materials, at the right time, and in the right quantity to meet production demands. Its key functions revolve around planning material needs based on forecasts and existing orders.
It achieves this by:
- Demand Forecasting: Predicts future material requirements using sales data and production plans.
- Inventory Management: Tracks current stock levels of all materials.
- Bill of Materials (BOM) Explosion: Determines the raw materials and components needed to manufacture finished products.
- MRP Run: Calculates net material requirements, considering existing inventory and scheduled receipts.
- Procurement Proposals: Generates purchase requisitions for externally procured materials and planned orders for internally manufactured items. It essentially answers: What do I need to buy? What do I need to make? When do I need it?
11. Explain the difference between consumption-based planning and MRP in SAP MM. Make it simple please.
Consumption-based planning focuses on historical consumption data to forecast future material needs. It's reactive, meaning it triggers replenishment when stock falls below a defined reorder point. Think of it like automatically ordering printer paper when the supply gets low based on how much you've used in the past.
MRP (Material Requirements Planning), on the other hand, is a proactive, demand-driven approach. It uses sales orders, production plans, and Bills of Materials (BOMs) to calculate precisely what materials are needed and when. It considers existing inventory, lead times, and dependencies between materials to create a detailed production and procurement schedule. MRP calculates what to procure and when based on actual or planned demand. Consumption-based planning reacts after the stock runs low.
12. How do you set up and use batch management in SAP MM, and why is it important for certain materials? KISS - Keep It Simple Stupid.
To set up batch management in SAP MM: 1. Activate batch management in the material master (purchasing view or plant data/storage view). 2. Define batch-specific characteristics if needed (using transaction CT04). 3. Configure batch determination strategies if automatic batch selection is required.
It's important for materials requiring traceability (e.g., pharmaceuticals, food) to track expiry dates, origins, or quality. Batch management helps with recalls, quality control, and ensures compliance.
13. Describe the purpose and functionality of the service entry sheet in SAP MM. Simple explaination.
The service entry sheet (SES) in SAP MM serves to formally document and approve the performance of services procured from external vendors. It acts as a confirmation that the agreed-upon services have been rendered according to the purchase order terms.
Functionally, after a service is performed, the SES is created referencing the purchase order. It specifies the quantity and description of the services delivered. Once approved by the relevant personnel, it forms the basis for invoice verification and payment to the vendor. The SES ensures that payment is made only for services actually received and accepted, providing a control mechanism in the procurement process.
14. What is the role of release strategies in SAP MM, and how do you configure them for purchase requisitions and purchase orders? Make it so a child understands.
Imagine you want to buy a toy. You can't just buy it yourself if it's expensive, right? You need your parents' permission. In SAP MM, release strategies are like that permission process for buying things for the company. They make sure the right people approve a purchase before it's made. This is especially important for things like Purchase Requisitions (a request to buy something) and Purchase Orders (the actual order to buy something). It helps control spending and make sure everyone follows the rules.
To configure them, you basically tell SAP: 'If the purchase is for this amount of money, then these people need to approve it.' You set up steps, and each step might require someone with a certain job title to say 'yes'. For example, if a purchase requisition is for more than $1000, it might need approval from the manager and the finance department. You use configuration transactions in SAP to define these steps and who needs to approve at each step, by specifying release codes and release groups, and linking characteristics like the document type or total value to trigger the release process. It is then linked to the purchase requisition document type. Similar steps are followed for purchase orders. It uses tables like T16FC, T16FB.
15. Explain the purpose of info records in SAP MM, and how they are used to store vendor and material information. KISS - Keep It Simple Stupid.
Info records in SAP MM are like cheat sheets that store buying info for specific materials from specific vendors. They link a material to its vendors, and keep track of things like: vendor's price, delivery times, and the vendor's material number. This avoids re-entering the same information every time you order.
Basically, it helps streamline procurement by:
- Storing standard prices and conditions.
- Tracking vendor-specific data (like their material numbers).
- Documenting the last purchase order for a material from a vendor.
- Helping automate purchase order creation.
16. How do you handle returns to vendor in SAP MM, and what are the key transactions involved? Explain like I am five.
Imagine you bought a toy, but it's broken. Sending it back is a return to the vendor! In SAP, it's similar. When goods are not good, you can send them back to the person who sold them. SAP has special buttons (transactions) to help you do this. You basically tell SAP 'Hey, this item is going back', then SAP does some paperwork to record it (creating a return purchase order, then doing a goods receipt reversal).
Key 'buttons' (transactions) are MIGO
(for returning the goods - goods receipt reversal) and MR8M
(to cancel the invoice). A return purchase order is created using ME21N
. You are telling SAP that the item is going back so you don't pay for it, or to get your money back if you already paid.
17. Describe the process of invoice verification in SAP MM and how it relates to the purchase order and goods receipt. Make it simple.
Invoice verification in SAP MM is the process of checking if an invoice from a vendor is correct before paying it. It's tightly linked to the Purchase Order (PO) and Goods Receipt (GR). The system compares the invoice details (price, quantity, etc.) with the PO and GR documents.
The process generally involves these steps:
- The vendor sends an invoice.
- The invoice is entered into SAP.
- SAP automatically checks if the invoice matches the PO (what was ordered) and the GR (what was received).
- If there are discrepancies (e.g., the price is different, or the quantity doesn't match), the system flags it for investigation.
- If everything matches, the invoice is approved for payment.
18. What are the key functionalities of the reporting tools in SAP MM, and how can they be used to analyze procurement data? Simple explaination.
SAP MM reporting tools provide key functionalities to analyze procurement data, including:
- Standard Reports: Pre-built reports for common analyses like purchase order tracking, inventory levels, and vendor performance.
- Custom Reports: Ability to create tailored reports based on specific needs using tools like SAP Query or ABAP programming.
- Analytics: Integration with SAP BW or other business intelligence platforms for advanced data analysis and visualization.
These tools enable users to:
- Monitor procurement processes: Track PO status, identify bottlenecks, and improve efficiency.
- Analyze spending patterns: Identify cost-saving opportunities and negotiate better contracts.
- Evaluate vendor performance: Assess vendor reliability, quality, and pricing to make informed sourcing decisions.
19. Explain the concept of 'goods receipt' in SAP MM. Why is it important?
A goods receipt in SAP MM is the process of accepting delivery of goods from a vendor or production order into the company's storage location. It's essentially the physical arrival of materials and the recording of this event in the SAP system. This process updates inventory quantities and values, providing a real-time view of available stock.
Goods receipts are crucial for several reasons: * Inventory Accuracy: Ensures that the system reflects the correct quantity of materials on hand. * Financial Accuracy: Updates the general ledger with the value of the received goods. * Material Availability: Enables accurate planning and procurement processes. * Vendor Payment: Often triggers the invoice verification process, leading to payment to the vendor. * Quality Assurance: Goods receipt is often tied to Quality inspections.
20. If a purchase order has already been created, can the price be changed, and how?
Generally, changing the price on a purchase order (PO) after it's created depends on the system and approval workflows in place. In many systems, directly changing the price on an approved PO is restricted to maintain an audit trail.
Here's how it's commonly handled:
- Amendment or Revision: A new version of the PO is created with the updated price. This preserves the original PO for historical records while reflecting the change. This will usually require re-approval.
- Change Request: A change request process is initiated. This may trigger an approval workflow where relevant stakeholders (e.g., purchasing, finance) review and approve the price change.
- Credit/Debit Memos: If the PO is already invoiced, then credit and debit memos are often used to correct the amount owed.
21. Can you have multiple delivery dates in one purchase order? Explain the process to do this.
Yes, a purchase order (PO) can have multiple delivery dates. This is common when ordering a large quantity of goods that the supplier cannot deliver all at once, or when the buyer needs the goods in stages.
The process typically involves specifying different line items on the PO for the same product, each with its own quantity and delivery date. The PO system should support this, allowing you to define a 'schedule' for each item. For example, you might order 100 units of a product. Line item 1 could specify 50 units to be delivered on date A, and line item 2 could specify the remaining 50 units to be delivered on date B. Some systems also allow scheduling within a single line item. The supplier then acknowledges these scheduled deliveries and ships accordingly.
22. What are some reasons a goods receipt might be blocked in SAP MM?
A goods receipt might be blocked in SAP MM for several reasons. One common reason is quality issues. If the goods do not meet the pre-defined quality standards during inspection, the goods receipt can be blocked preventing further use. Another reason is discrepancies between the purchase order and the delivery. This could be quantity deviations, wrong materials delivered, or other inconsistencies that require investigation before the goods can be accepted. Goods can also be blocked because of missing information, such as incorrect or missing vendor information, or certification.
Furthermore, the blocking could be due to inconsistencies found during the automatic posting of the GR/IR account. If the system detects errors during the automatic account assignment process, the goods receipt may be blocked to prevent incorrect financial postings. Another reason could be due to storage location restrictions or capacity issues; if there isn't enough space in the designated storage location, the goods receipt can be blocked until the issue is resolved.
23. In SAP MM, what are the different ways you can evaluate vendors, and why is vendor evaluation important?
In SAP MM, vendor evaluation can be done using several methods, primarily through a questionnaire-based system or a performance-based system. The questionnaire-based system involves sending questionnaires to different departments within the company to gather feedback on the vendor's performance across various criteria. The performance-based system relies on automatically evaluating vendors based on key performance indicators (KPIs) tracked within the system, such as delivery time, quality of goods, and price adherence. Some common KPIs include: Price Level, Quality, Delivery Reliability, Quantity Reliability, and Compliance. Both methods can be combined for a more comprehensive evaluation.
Vendor evaluation is crucial for several reasons. It helps in identifying reliable and high-performing vendors, leading to better procurement decisions. This, in turn, improves the quality of goods and services received, ensures timely delivery, and optimizes costs. Effective vendor evaluation also helps in mitigating risks associated with supply chain disruptions and fosters stronger, more collaborative relationships with key vendors. Ultimately, it contributes to improved efficiency and profitability for the organization.
SAP MM interview questions for experienced
1. How would you approach optimizing a slow-running MRP process in a complex manufacturing environment?
Optimizing a slow MRP process in a complex manufacturing environment requires a multi-faceted approach. First, a thorough analysis to identify bottlenecks is critical. This includes reviewing MRP parameters (lead times, safety stock, lot sizing), BOM accuracy, and routing data. Improving data accuracy is often the first step, as MRP's output quality depends on its input. We should also profile the MRP run using monitoring tools or code-level instrumentation to precisely pinpoint the slowest routines or database queries and then optimize them.
Next, consider process improvements and system configuration adjustments. For example, explore parallel processing capabilities if available in the MRP system. Optimize database queries used by the MRP system using indexing and query optimization techniques. Evaluate the possibility of breaking down the large MRP run into smaller, more manageable chunks based on product families or work centers, provided dependencies allow it. Finally, explore upgrading hardware (CPU, memory, storage) or migrating to a more scalable MRP system if the current infrastructure is insufficient despite other optimizations.
2. Describe your experience with implementing and configuring advanced planning and optimization (APO) modules integrated with SAP MM.
My experience with APO integration with SAP MM primarily involves Demand Planning (DP) and Supply Network Planning (SNP) modules. I've configured DP to generate accurate forecasts using historical sales data from MM, incorporating statistical forecasting techniques and promotional planning. For SNP, I've worked on optimizing the supply chain by considering material availability from MM, production capacities, and transportation constraints. I've implemented planning strategies, such as push and pull systems, based on the specific requirements of materials managed in MM, focusing on minimizing inventory holding costs while meeting customer demand.
Specifically, I've utilized CIF (Core Interface) to transfer master data and transactional data between SAP ECC (MM) and APO. This includes material master data, purchase orders, sales orders, and stock levels. I have configured CIF integration models to filter relevant data, ensuring data consistency between the two systems. I also have experience in troubleshooting CIF errors and optimizing data transfer performance to minimize delays in the planning process. My work has involved configuring release strategies, safety stock levels, and deployment heuristics within APO, all driven by parameters and data originating from SAP MM.
3. Can you elaborate on your experience managing a large-scale SAP MM implementation or upgrade project?
In my previous role at Acme Corp, I spearheaded a full SAP MM implementation across five manufacturing plants. This involved managing a team of 15 consultants and internal stakeholders, coordinating data migration from legacy systems, configuring MM modules to align with business processes (procurement, inventory management, invoice verification), and ensuring seamless integration with FI/CO. Key challenges included user training and data cleansing, which we addressed through targeted workshops and data governance policies. I was also responsible for risk management, budget control (around $2M), and project timeline adherence, ultimately delivering the project on time and within budget.
During the upgrade from ECC 6.0 to S/4HANA, I focused on minimizing disruption to ongoing operations. This involved a phased approach, starting with a sandbox environment for testing and issue resolution. We utilized the SAP Readiness Check to identify potential compatibility issues and proactively addressed them. A critical aspect was ensuring the upgrade adhered to SOX compliance, which required meticulous documentation and testing. I also managed the change management process, communicating updates and providing support to end-users throughout the transition, which resulted in a smooth transition with minimal downtime.
4. Explain how you've used SAP MM to improve inventory accuracy and reduce stockouts in a high-volume distribution center.
In a high-volume distribution center, I leveraged SAP MM functionalities to improve inventory accuracy and reduce stockouts. I implemented cycle counting procedures using SAP's physical inventory documents, configuring the system to automatically generate cycle count requests based on ABC analysis and stock turnover rates. We also utilized the RF (Radio Frequency) functionality within MM to ensure real-time updates during goods receipt, putaway, and picking processes, minimizing discrepancies between physical stock and system records. By implementing stringent GR/IR (Goods Receipt/Invoice Receipt) reconciliation processes, we were able to promptly resolve any quantity or value differences, preventing stock inaccuracies and potential stockouts. Finally, I worked with the ABAP team to customize reports to track key performance indicators (KPIs) such as inventory turnover, stockout rates, and cycle count accuracy, enabling data-driven decision-making and continuous improvement. We used consignment stock functionality with vendors to avoid stockout situations for high-value material or material with long lead times.
5. How have you handled integration challenges between SAP MM and other SAP modules like FI/CO, SD, and PP?
I've addressed SAP MM integration challenges with FI/CO, SD, and PP through a combination of configuration, ABAP development, and IDoc monitoring. For example, with FI/CO, I ensured proper account determination by configuring valuation classes and GL account assignments based on material types and movement types. I've used enhancement points and BAPIs to automatically create accounting documents upon goods receipt or invoice verification. Similarly, for SD integration, I've configured copy control settings to ensure accurate sales order data flows to purchasing documents. Furthermore, I've worked on PP integration to ensure MRP creates planned orders and purchase requisitions based on demand, configuring the necessary settings in the material master and production planning parameters. Monitoring IDocs through transaction WE02 has been crucial to identify and resolve data transfer issues between modules.
6. Describe a time when you had to troubleshoot a complex pricing issue in SAP MM involving multiple condition types and discounts.
In a previous role, we encountered a complex pricing issue where a material was being priced incorrectly in SAP MM. After initial analysis, it was clear that the issue stemmed from the interaction of multiple condition types: a base price condition, a quantity-based discount, and a customer-specific discount. The customer was not receiving the correct combined discount.
I troubleshooted this by first recreating the scenario in a test environment. Then, using transaction VK13, I examined the individual condition records to verify their correctness and validity periods. I also reviewed the pricing procedure (transaction M/08) to understand the sequence and dependencies of the different condition types. The key was understanding the 'Calculation type' and 'Condition base value' fields within the pricing procedure. I discovered that the customer-specific discount was being applied before the quantity discount, leading to an inaccurate final price. The fix involved adjusting the pricing procedure to ensure the quantity discount was calculated first. After testing, the pricing was corrected.
7. Explain your experience with vendor evaluation and performance monitoring within SAP MM. What KPIs did you track?
In SAP MM, vendor evaluation and performance monitoring are crucial for maintaining supply chain efficiency. My experience includes developing and executing vendor evaluation processes, using SAP's standard functionalities like vendor evaluation based on price, quality, and delivery. I've also customized scoring models to align with specific business requirements, incorporating factors such as responsiveness and technical support. Performance monitoring involved regularly tracking KPIs such as on-time delivery rate, quality acceptance rate, price variance, and invoice accuracy.
Specifically, I utilized SAP's standard reports and created custom reports using ABAP to monitor these KPIs. I would then analyze the data to identify underperforming vendors and work with them to improve their performance through corrective action plans. In some instances, poor performance led to contract renegotiations or even vendor delisting. I also employed vendor scorecards within SAP to visualize and communicate vendor performance to both internal stakeholders and the vendors themselves, fostering transparency and accountability.
8. How would you design a process for handling consignment inventory in SAP MM, ensuring accurate tracking and settlement?
Consignment inventory in SAP MM can be handled using a special procurement type. First, a consignment info record is created, linking the vendor and material. Goods receipt is then posted using movement type 101 K. The inventory is now stored at your location but still owned by the vendor. When you consume the material, a goods issue is posted using movement type 201 K, transferring ownership and triggering settlement. Settlement is performed via MRKO, which generates a liability to the vendor for the consumed quantity.
To ensure accurate tracking and settlement, configure tolerances for quantity and price differences in MM configuration. Regularly reconcile consignment stock balances with the vendor. Use batch management for better traceability of consignment materials. MRKO should be executed periodically. Consider implementing workflow for MRKO approvals to enhance control.
9. Describe your experience with implementing and managing a service procurement process within SAP MM.
My experience with service procurement in SAP MM includes configuring and managing the entire process flow, from service master creation to invoice verification. I've worked with service entry sheets (SES), ensuring proper approval workflows based on predefined limits and user roles. I've also configured account assignment categories to ensure accurate cost allocation to the correct cost centers or projects. A key aspect involved integrating service procurement with other modules, such as Finance and Controlling, to maintain data consistency and ensure timely payment processing.
Furthermore, I have experience in troubleshooting issues related to service procurement, such as SES rejections, incorrect pricing, and discrepancies between the SES and the invoice. I've also been involved in customizing the service procurement process to meet specific business requirements, including developing custom reports to monitor service spend and vendor performance. I have worked with both standard and limit purchase orders, adapting the process to different service procurement scenarios.
10. How have you used SAP MM to support lean manufacturing principles and just-in-time inventory management?
I've used SAP MM in several ways to support lean manufacturing and JIT. For example, I configured MRP settings to optimize inventory levels, reducing waste and storage costs. This included setting reorder points based on actual demand and lead times, as well as utilizing consumption-based planning to automatically trigger purchase requisitions only when needed.
Furthermore, I've implemented strategies like vendor-managed inventory (VMI) using scheduling agreements in SAP MM. This helps to synchronize material flow with production requirements, ensuring timely delivery of materials directly to the shop floor, minimizing inventory holding and improving production efficiency. I also configured kanban replenishment strategies within SAP MM to further optimize material availability at the point of use.
11. Explain your approach to data migration and cleansing during an SAP MM implementation or upgrade.
My approach to data migration and cleansing in an SAP MM implementation or upgrade involves a structured methodology. First, I perform a thorough data assessment to understand the quality and structure of the legacy data, identifying gaps and inconsistencies. This includes profiling the data to understand its distribution and identifying potential data quality issues. Next, based on the assessment, I define data cleansing rules and transformations needed to map the legacy data to the SAP MM data model. I then use tools like SAP Data Services or custom ABAP programs to perform the actual data cleansing and transformation. A critical step is rigorous data validation after migration, comparing the migrated data with the original source to ensure accuracy and completeness. Throughout the process, I emphasize close collaboration with business stakeholders to ensure the migrated data meets their requirements and supports their business processes.
I focus on key areas like vendor master data, material master data, purchasing info records, and source lists. For example, ensuring that vendor data includes correct addresses and payment terms, material data has accurate descriptions and units of measure, and that purchasing info records reflect up-to-date pricing and lead times. During the cleansing process, I prioritize de-duplication of records, standardization of values, and enrichment of data where necessary. A typical scenario would involve using a staging area for the transformed data before the final migration, allowing for multiple rounds of validation and cleansing before loading the data into the production SAP MM system.
12. How would you configure SAP MM to support different procurement scenarios, such as direct materials, indirect materials, and capital equipment?
To configure SAP MM for different procurement scenarios, you'd primarily leverage document types, account assignment categories, and item categories. For direct materials, use standard purchase orders (NB document type) with account assignment category typically blank (or K for cost center if consumed directly) and standard item category. Indirect materials often use document type NB, account assignment categories like K (cost center), U (unknown), or C (sales order), and standard item category. Capital equipment utilizes document type FO (framework order, if applicable, or NB), account assignment category A (asset), and often item category D (service) if installation is involved or standard. Furthermore, you can configure different release strategies based on the document type and value, ensuring appropriate approvals for each scenario.
13. Describe your experience with implementing and using SAP Ariba for procurement processes integrated with SAP MM.
My experience with SAP Ariba and SAP MM integration involves implementing and utilizing Ariba's procurement solutions within the SAP MM landscape. I've worked on projects that integrated Ariba Sourcing, Ariba Buying, and Ariba Supplier Network with SAP MM, focusing on streamlining the procure-to-pay process. This included configuring data transfer mechanisms, such as CIF (Core Interface) or direct integration via APIs, to synchronize master data (e.g., materials, vendors) and transactional data (e.g., purchase orders, goods receipts) between the two systems.
I've also been involved in customizing Ariba's workflows to align with specific business requirements and integrating Ariba with SAP MM's invoice verification process to automate invoice matching and payment. My role involved troubleshooting integration issues, optimizing data flows, and collaborating with cross-functional teams (including procurement, IT, and finance) to ensure a seamless and efficient procurement process. I have experience working with Ariba cloud integration gateway as well as understanding the different Ariba modules involved.
14. How have you used SAP MM to manage contracts and agreements with vendors, ensuring compliance and cost control?
In my previous roles, I've used SAP MM extensively to manage vendor contracts. I've utilized the outline agreement functionality, particularly contract and scheduling agreement types, to define terms, pricing, and delivery schedules with vendors. I've ensured compliance by maintaining accurate contract data within SAP, including validity periods, payment terms, and agreed-upon service levels. The system's reporting capabilities allowed me to track contract utilization, identify potential deviations from agreed-upon terms, and proactively address any compliance issues.
For cost control, I've leveraged SAP MM's pricing conditions and release strategies. By configuring appropriate price conditions, I could effectively negotiate and maintain competitive pricing. Release strategies, linked to purchasing documents, enabled a multi-level approval process to ensure that all purchases aligned with budget constraints and procurement policies. I also regularly performed spend analysis using SAP MM data to identify opportunities for cost savings through vendor consolidation or renegotiation of existing contracts.
15. Explain your experience with setting up and managing release strategies for purchase orders in SAP MM.
I have experience configuring and managing release strategies for purchase orders in SAP MM. I've worked with defining release codes, release groups, release indicators, and release prerequisites to establish multi-level approval workflows. This includes mapping organizational data such as purchasing organization, purchasing group, and material group to determine release determination. I've also been involved in setting up workflow rules and alerts to notify approvers when a purchase order requires their attention.
Specifically, I've utilized the configuration nodes in SPRO to define release strategies based on characteristics like total order value, account assignment category, and document type. My experience includes troubleshooting issues related to release strategy determination, such as incorrect configuration or missing data in the purchase order. I've also worked on modifying existing release strategies to accommodate changing business requirements, ensuring proper documentation and testing throughout the process.
16. How would you configure SAP MM to handle intercompany stock transfers between different plants or company codes?
To configure intercompany stock transfers in SAP MM, you need to set up several key elements. First, create customer and vendor master records for the receiving and supplying plants, ensuring they are assigned to the respective company codes. Define a stock transport order (STO) document type specifically for intercompany transfers. Configure the delivery type (NLCC) and assign it to the STO document type.
Next, maintain the shipping data for the supplying plant, including the sales organization, distribution channel, and division. Define the item category and schedule line category for the STO. Configure pricing conditions to determine the transfer price between company codes. Finally, set up the relevant account determination using OBYC for the goods issue and goods receipt postings to ensure proper financial accounting. Optionally, utilize IDocs or EDI for automated processing.
17. Describe your experience with implementing and using SAP Fiori apps for procurement processes within SAP MM.
I have experience implementing and using SAP Fiori apps to streamline procurement processes within SAP MM. Specifically, I've worked with apps like 'My Purchase Requisitions', 'Approve Purchase Requisitions', and 'Track Purchase Orders'. My work involved configuring these apps, customizing them to meet specific business needs (like adding custom fields), and integrating them with other SAP modules. I also have experience with troubleshooting Fiori app issues and providing end-user training.
Furthermore, I've been involved in enhancing the user experience by tailoring the Fiori Launchpad and implementing role-based access. This included defining specific catalogs and groups for different user roles involved in the procurement process, ensuring that users only have access to the apps and information relevant to their responsibilities. For example, requisitioners could easily create and track their requests, while approvers could efficiently review and approve them via mobile devices.
18. How have you used SAP MM to support sustainability initiatives, such as tracking environmental impact and promoting responsible sourcing?
In my previous role, I utilized SAP MM to support sustainability initiatives in several ways. I configured the system to track environmental impact by integrating material master data with environmental performance indicators. This allowed us to monitor the carbon footprint and water usage associated with specific materials and suppliers. We leveraged batch management and reporting functionalities to trace the origin and processing of materials, ensuring compliance with responsible sourcing standards. I also used MM to manage the procurement of eco-friendly materials by creating specific material groups and preferred vendor lists based on sustainability certifications.
19. Explain your experience with setting up and managing automatic account determination in SAP MM.
My experience with automatic account determination in SAP MM involves configuring the system to automatically post goods movements to the correct G/L accounts. I have worked with transaction OBYC to configure valuation grouping codes, valuation classes, and account grouping for movement types. I understand the importance of correctly assigning these parameters to ensure accurate financial postings during goods receipt, goods issue, and other inventory transactions. I also have experience troubleshooting account determination issues by analyzing the account determination analysis tool in SAP, and also using debuging tools to analyse the account determination process by debugging the code.
Specifically, I have configured BSX (Inventory Posting), WRX (GR/IR clearing account), GBB (Offsetting entry for inventory posting), and PRD (Price differences) transaction keys. I have also implemented solutions to handle scenarios where specific materials or material groups require different account assignments based on plant or other organizational levels. This often involves creating new valuation classes or modifying existing account determination settings within OBYC to meet specific business requirements. I have been involved in unit testing the configuration and assisting the users in their testing as well.
20. How would you configure SAP MM to handle returns and credit memos from vendors?
To configure SAP MM to handle returns and credit memos from vendors, you would first define return reasons in configuration (SPRO > MM > Purchasing > Purchase Order > Returns Order > Define Reasons for Returns). This allows you to track why a return is being processed. For returns, create a return purchase order (PO) - either manually (ME21N) or through a goods receipt reversal (MBST) or subsequent adjustment (MIGO). Ensure the 'Return PO' indicator is set in the PO item details. The goods movement 161 (Return delivery to vendor) will automatically trigger upon posting the goods receipt against the return PO. You can create credit memos related to vendor returns using transaction MIRO, referencing the return PO or the original invoice as appropriate. The key is to match the quantity and price for reconciliation.
For credit memos not related to returns, create a standard credit memo in MIRO. Choose 'Credit Memo' as the transaction type. Ensure the invoice reference is accurate. For both types of credit memos, verification of prices and quantities against the vendor's credit memo is crucial before posting. Blocking reasons can be configured to enable workflow around credit memo approval.
21. Describe your experience with implementing and using SAP S/4HANA for procurement processes within SAP MM.
I have experience implementing and using SAP S/4HANA for procurement processes, focusing on the Materials Management (MM) module. My involvement has included configuring master data relevant to procurement, such as material master, vendor master, and purchasing info records. I have worked with the creation of purchase requisitions, purchase orders, and goods receipts, and also configured workflows for PO approval based on defined parameters like value or material group.
Furthermore, I've worked with functionalities like source determination, automatic PO generation, and invoice verification. I also have experience with reporting on procurement activities, utilizing SAP Analytics Cloud (SAC) connected to S/4HANA to build dashboards for tracking key procurement metrics like spend analysis and vendor performance. I understand the benefits of S/4HANA's simplified data model and Fiori-based user interface in streamlining procurement operations.
22. How have you used SAP MM to manage quality inspections and vendor audits?
In SAP MM, I've used quality info records to link vendors with specific quality requirements and inspection plans. During goods receipt, inspection lots are automatically triggered based on these settings, ensuring materials undergo predefined quality checks. I've configured inspection plans with specific test characteristics and acceptance criteria, and then recorded inspection results within SAP. I've also worked with vendor evaluation functionalities to track audit scores and inspection outcomes, influencing future sourcing decisions. This involved configuring vendor evaluation criteria based on quality performance metrics derived from inspection results. Furthermore, I've utilized QM notifications to address non-conformances detected during inspections, triggering corrective actions and process improvements with vendors.
23. Explain your experience with setting up and managing material master data in SAP MM, including classification and characteristic-based configuration.
I have extensive experience in setting up and managing material master data in SAP MM. This includes creating new material masters, maintaining existing ones, and ensuring data accuracy and consistency across the system. I'm familiar with various material types and their specific configurations. I've also worked with classification and characteristic-based configuration to categorize materials based on their properties and attributes. This involved creating classes and assigning characteristics to them, then classifying materials accordingly. This ensures easier reporting and allows for searching of materials based on specific attributes. I have experience with maintaining material master data using mass maintenance tools, ensuring consistency during large scale material updates.
24. How would you approach optimizing the purchasing workflow to improve efficiency and reduce manual intervention?
To optimize the purchasing workflow, I would focus on automation and streamlining processes. This would involve:
- Implementing an automated purchase order system: This could automatically generate POs based on pre-defined thresholds for inventory levels, integrating with inventory management and accounting systems.
- Automating invoice processing: Using OCR and machine learning to automatically extract data from invoices and match them to POs and receipts, reducing manual data entry and errors.
- Negotiating favorable terms with suppliers: Securing volume discounts or other advantageous pricing arrangements to reduce costs. Moving to blanket purchase orders for recurring needs.
- Centralizing purchasing: Consolidating purchasing activities across different departments to leverage economies of scale and improve negotiation power.
- Using spend analytics to identify areas for improvement: Analyzing purchasing data to identify opportunities to reduce costs, improve efficiency, and mitigate risks.
- Establishing clear approval workflows: Implementing a system for routing purchase requests to the appropriate approvers based on pre-defined rules and thresholds, ensuring timely and efficient approvals.
SAP MM MCQ
Which account assignment category is typically used for direct consumption to a cost center without tracking inventory?
Which of the following statements best describes the primary purpose of a stock transport order (STO)?
What field in the Material Master record defines the number of workdays required after receiving materials from a vendor to make them available for use?
What is the key impact of activating Goods Receipt (GR)-based Invoice Verification in the material master record?
How does setting the 'Storage location MRP' indicator to '1 - Storage location stock excluded from planning' impact the material planning process?
Which of the following statements best describes the impact of the MRP type on the planning run?
Options:
What is the primary impact of activating batch management for a material on goods movements?
Which of the following statements best describes the impact of the valuation class in the material master record?
Options:
Which of the following statements BEST describes the impact of a 'Special Procurement Key' on the MRP planning run?
Which of the following statements correctly describes the primary impact of a movement type on inventory posting when performing a goods movement in SAP MM?
options:
Which of the following plant parameters, when configured, will cause the MRP run to create purchase requisitions directly instead of planned orders?
Which of the following best describes the primary function of a purchasing group in SAP MM?
Which of the following is a direct result of posting a Goods Receipt (GR) against a Purchase Order (PO) in SAP MM?
Which of the following statements BEST describes the impact of activating split valuation for a material?
Options:
Which of the following BEST describes the impact of tolerance keys defined in tolerance groups on the goods receipt process?
Which of the following is the primary function of a purchasing document type in SAP MM?
Which of the following configurations has a direct impact on the availability check during the creation of a purchase order?
What is the primary purpose of maintaining a source list in SAP MM?
What is the primary impact of an active inspection type in Quality Management (QM) during a goods receipt process?
Which of the following factors primarily determines the G/L accounts that are updated during a goods movement?
Which of the following is the primary impact of a Purchasing Info Record on the procurement process?
Which configuration setting in SAP MM is MOST directly responsible for determining the G/L accounts that are automatically debited or credited during a goods movement?
Which of the following is the primary impact of a release strategy defined for purchase requisitions?
What is the primary effect of the 'Goods Receipt Processing Time' field in the material master on the material's availability for use?
Which of the following statements BEST describes the impact of delivery tolerances defined in the material master on the goods receipt process?
Which SAP MM skills should you evaluate during the interview phase?
While a single interview can't reveal everything about a candidate, focusing on core skills is key. For SAP MM roles, certain competencies are more important than others. Let's explore the skills you should prioritize evaluating during the interview process.
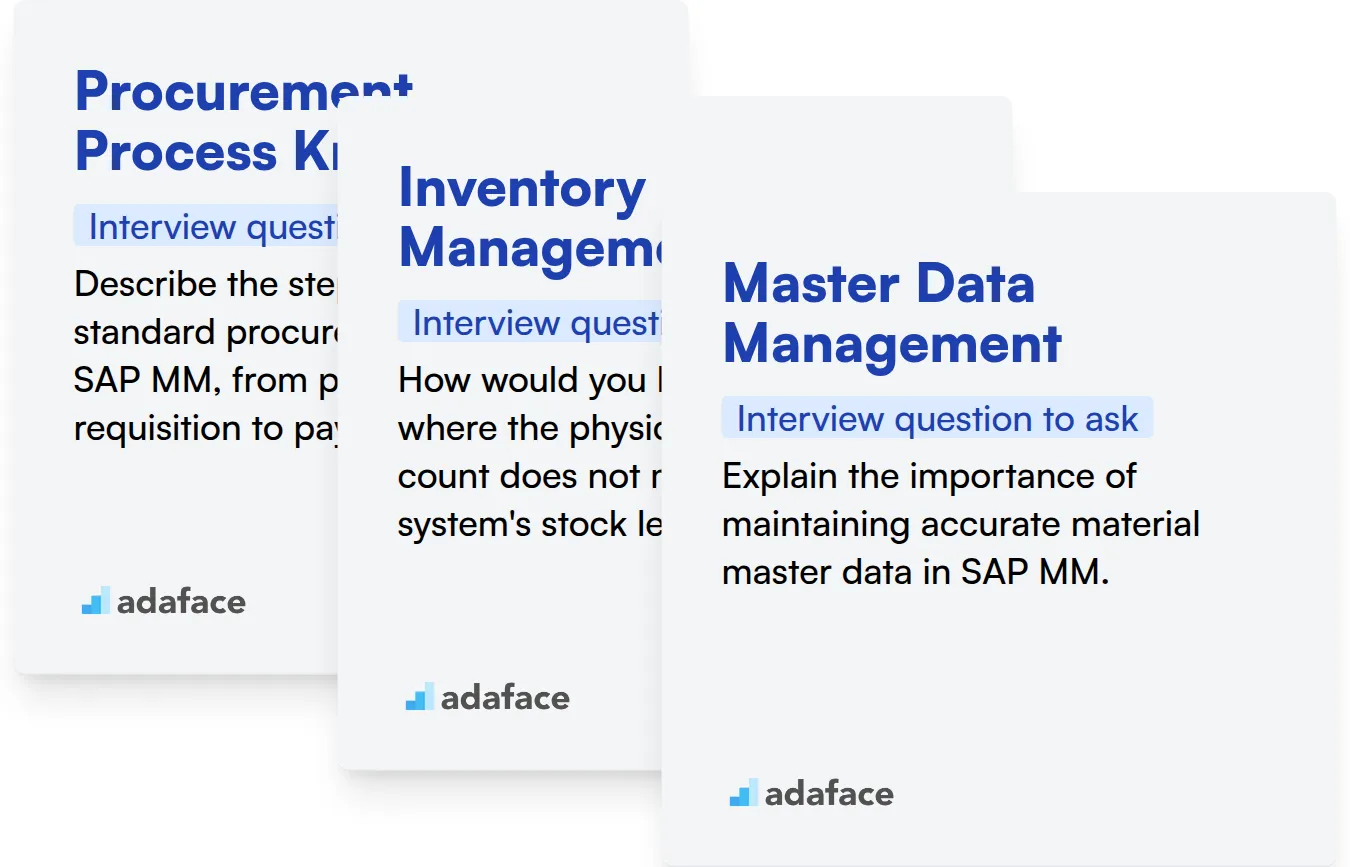
Procurement Process Knowledge
You can use assessment tests to gauge their familiarity with procurement processes. A test with relevant MCQs can quickly filter candidates with a solid base. Our SAP MM online test assesses knowledge of procurement processes, inventory management, and more.
To further assess their knowledge, ask targeted interview questions. These questions can help you understand how they apply their knowledge in real-world scenarios.
Describe the steps involved in the standard procurement cycle in SAP MM, from purchase requisition to payment.
Look for a clear, step-by-step explanation of the process. The candidate should be able to articulate the flow of information and documents between departments.
Inventory Management
See how well they know inventory management using a skill assessment. You can easily filter out candidates who don't know about inventory management. The SAP MM online test covers inventory management principles and SAP-specific configurations.
Dive deeper with interview questions focused on specific inventory scenarios. This will help you understand their practical experience and problem-solving abilities.
How would you handle a situation where the physical inventory count does not match the system's stock level?
The candidate should discuss the importance of investigating the discrepancy. They should also mention steps such as performing recounts, checking goods movements, and adjusting the inventory accordingly.
Master Data Management
Screen for candidates with strong master data knowledge using skill tests. See who actually knows this, and who just pretends to. Our SAP MM online test examines proficiency in master data creation, maintenance, and usage.
Ask targeted interview questions to assess their understanding of master data concepts. This will help you determine their ability to ensure data accuracy and consistency.
Explain the importance of maintaining accurate material master data in SAP MM.
The candidate should highlight how material master data impacts various processes. They should mention areas such as purchasing, inventory management, and material planning.
3 Tips for Using SAP MM Interview Questions
Now that you have a good set of SAP MM interview questions, let's discuss how to use them effectively. Here are a few tips to help you extract the most value from your interviews and identify the best candidates.
1. Leverage Skills Assessments for Objective Evaluation
Skills assessments offer a standardized way to evaluate a candidate's proficiency before the interview stage. This allows you to focus interview time on candidates who have already demonstrated a baseline level of competence.
Consider using Adaface's SAP MM Online Test to assess technical skills. You can also use other SAP related tests such as SAP FI test, SAP QM test or SAP ABAP test.
By integrating skills assessments, you can streamline your hiring process. This ensures that your interview time is spent on candidates with the strongest proven abilities.
2. Outline a Focused Set of Interview Questions
Time is limited during interviews, so it’s important to select a focused set of questions that target the most important skills. Carefully chosen questions will help you assess candidates on relevant areas within a tight timeframe.
Explore related areas like data analysis interview questions to assess analytical abilities. This helps you understand how candidates can leverage their SAP MM knowledge to derive insights.
Remember, the goal is to cover the most critical aspects of the role. This ensures you make informed decisions about a candidate's suitability.
3. Ask Follow-Up Questions to Uncover Deeper Understanding
Using the provided interview questions alone isn't always enough to gauge a candidate’s true abilities. Asking well-crafted follow-up questions is key to validate their understanding and experience.
For instance, after asking about a candidate's experience with inventory management in SAP MM, a follow-up could be: "Can you describe a time you had to resolve a discrepancy between physical stock and system records, and what steps did you take?" This helps reveal practical problem-solving skills and depth of knowledge.
Hire Top SAP MM Talent with Skills Tests and Targeted Interview Questions
When hiring for SAP MM roles, accurately assessing a candidate's skills is paramount. Using skills tests is the most effective way to achieve this. Consider using our SAP MM Online Test to quickly evaluate candidates.
Once you've used the skills test to identify your top candidates, you can invite them for targeted interviews. Ready to get started? Sign up for Adaface today and streamline your hiring process.
SAP MM Online Test
Download SAP MM interview questions template in multiple formats
SAP MM Interview Questions FAQs
Some beginner-level questions cover basic concepts such as material master, purchase orders, and goods receipt processes.
Experienced candidates can be evaluated on their knowledge of complex scenarios, such as inventory management, pricing procedures, and integration with other SAP modules.
Tips include preparing targeted questions, assessing practical knowledge with scenario-based questions, and evaluating problem-solving skills.
Targeted questions help identify candidates with the specific skills and experience needed for the SAP MM role, ensuring a better fit for the organization.
Common areas include procurement processes, inventory management, material master data, pricing conditions, and integration with finance and other modules.
A strong candidate possesses both theoretical knowledge and practical experience, demonstrating problem-solving capabilities and understanding of business processes within SAP MM.
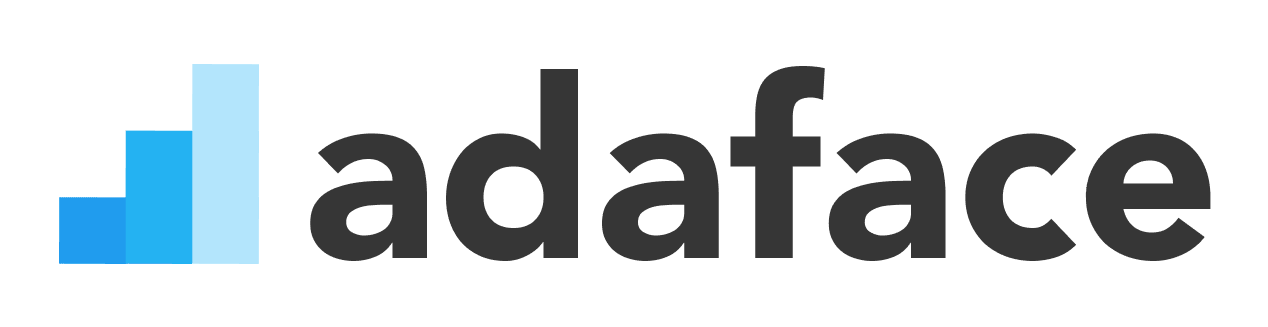
40 min skill tests.
No trick questions.
Accurate shortlisting.
We make it easy for you to find the best candidates in your pipeline with a 40 min skills test.
Try for freeRelated posts
Free resources
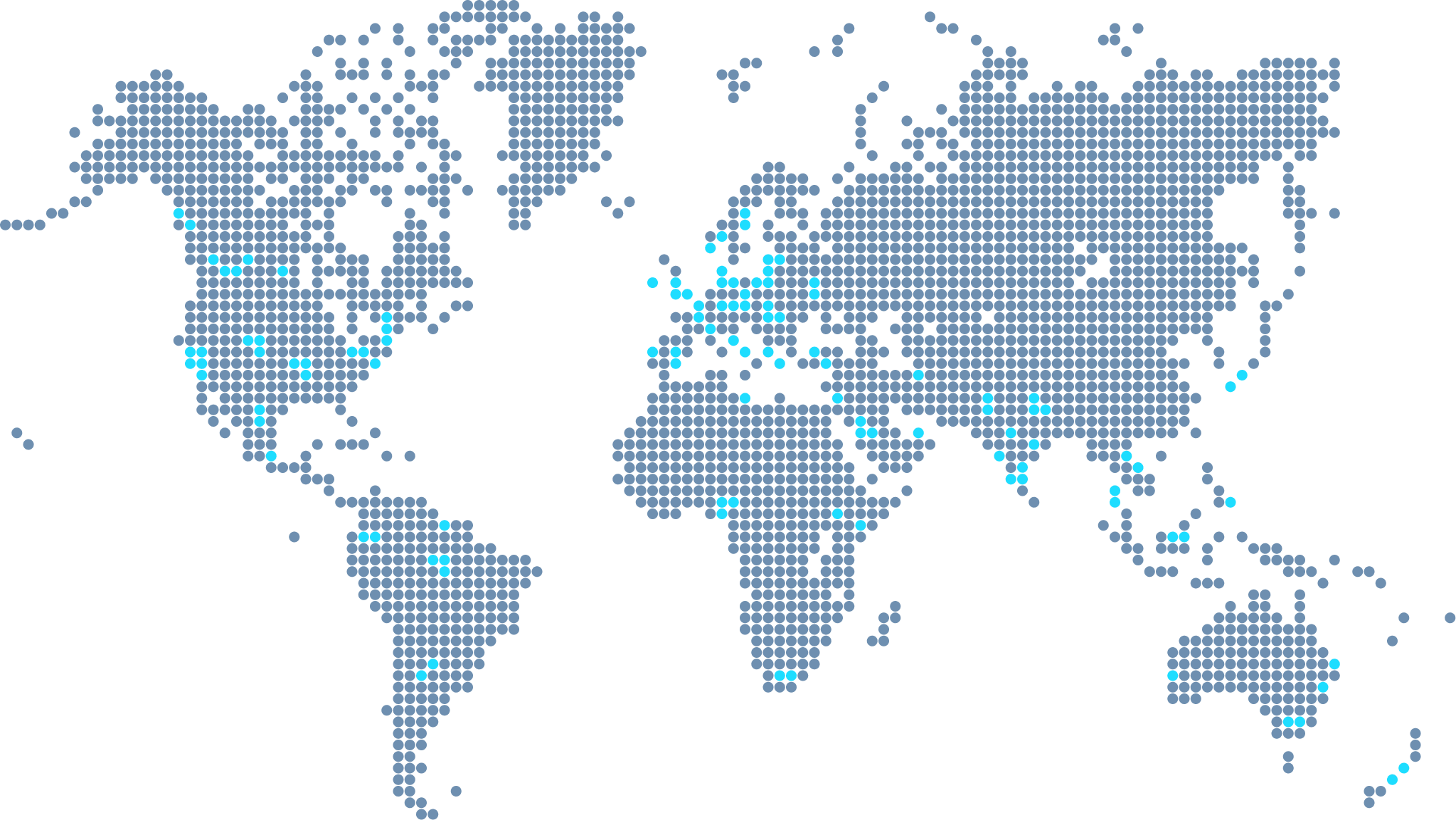
